EPDM Roofing: What It Is, Pros, Cons, Issues & More
By Jack Gray, Roof Online Editor • Last updated August 21, 2024
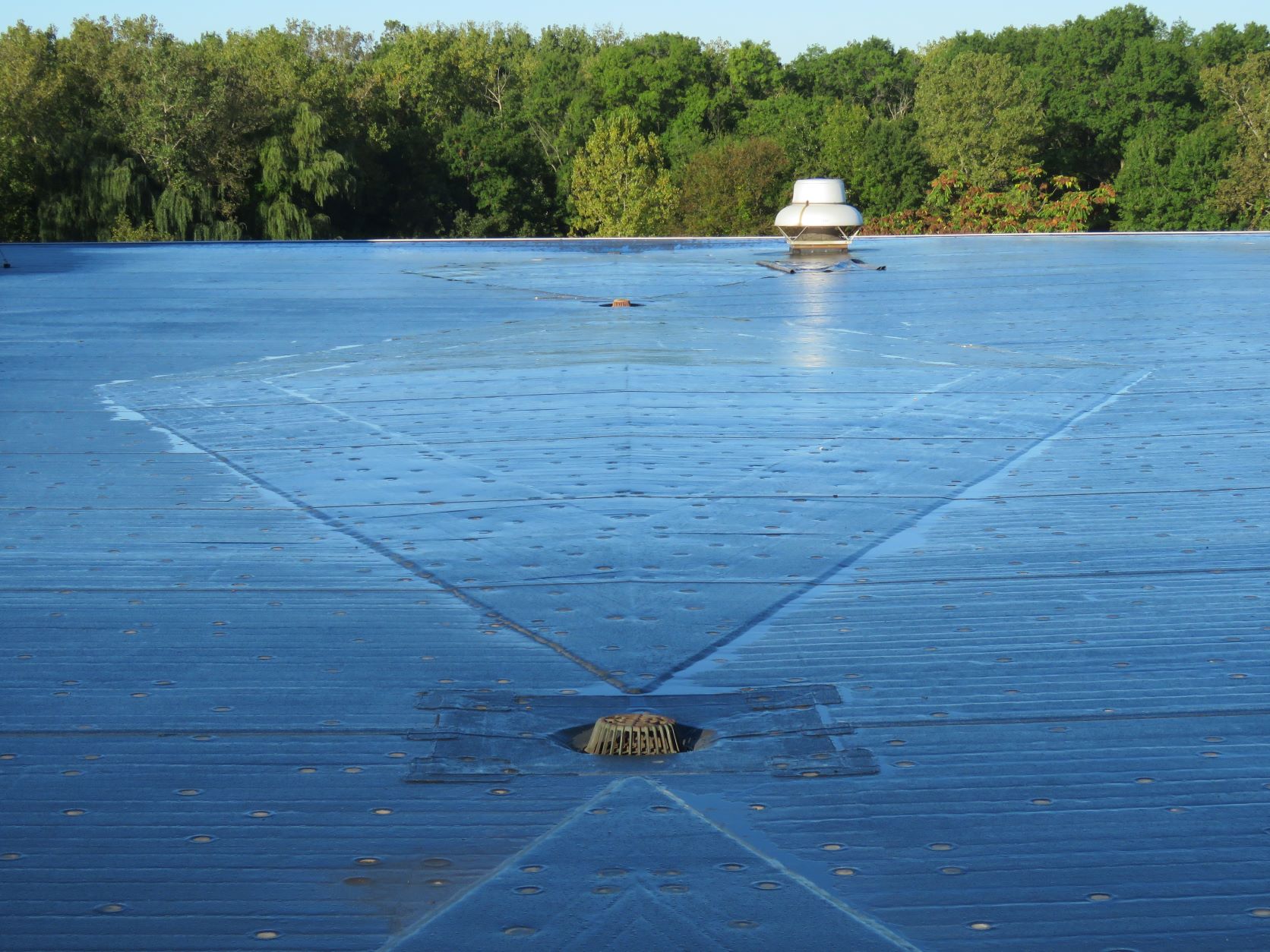
Table of Contents
- Introduction
- Pros & Cons of EPDM Roofing
- What is EPDM Rubber Roofing?
- Types of EPDM Roof Systems
- Characteristics of EPDM Membranes
- Lifespans of EPDM Rubber Roof Systems
- Things That Damage EPDM Rubber Roof Membranes
- Related Articles
- External Sources & References for EPDM Roofing Information
Introduction
We’re professional roof consultants – professional roof experts, you might say. Our clients include homeowners associations, corporate real estate asset managers, property managers, and facility directors.
As a part of our job, we decide whether our clients should use EPDM, TPO, or PVC for their new single-ply roof. If it’s EPDM, we decide what type of EPDM system to use based on location, budget, and desired length of service life.
We research and design EPDM roof systems for new roof installations and roof replacement projects. We inspect EPDM roofs and provide quality assurance during EPDM roof installations.
We’ve managed roof maintenance and leak response and repair programs that covered millions of square feet of EPDM roofing.
We know EPDM roofing pretty well, and we thought we would share some helpful information about EPDM here on our website.
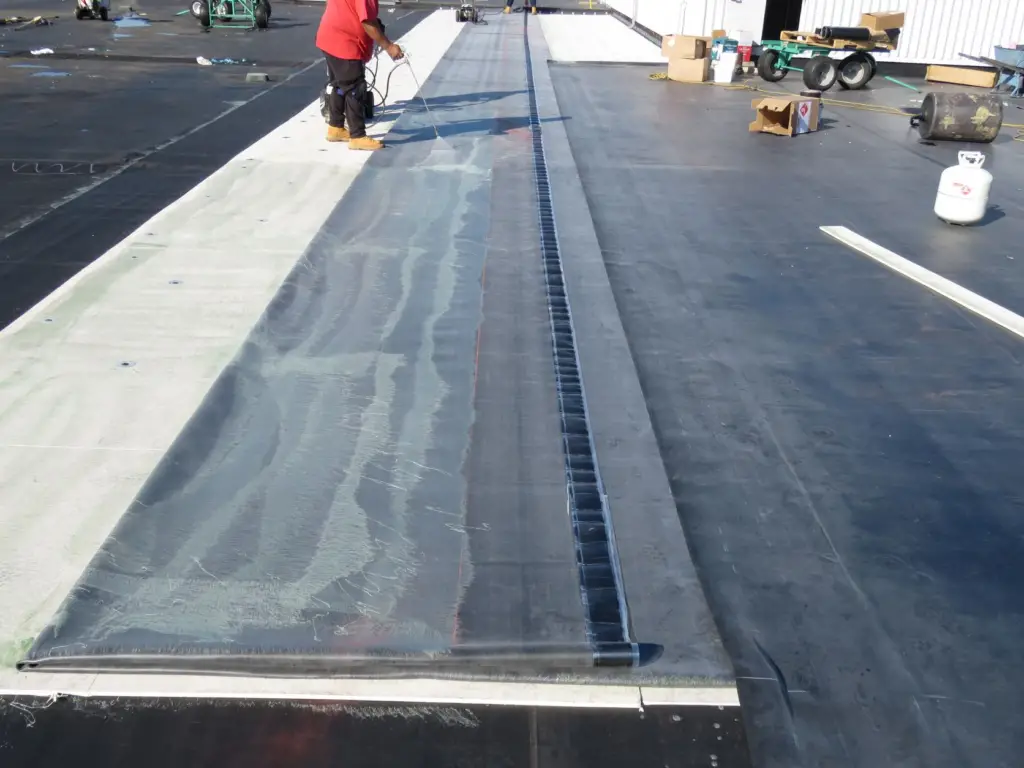
Pros & Cons of EPDM Roofing
If you’re just skimming this article to get a general sense of the advantages and disadvantages of an EPDM roof, here’s a short overview of the strong points and weak points of EPDM roofing. We get into more depth in the rest of article.
Pros of EPDM Roofing
Cool Roof
White EPDM roof membranes are available and they come with a white reflective surface for energy savings, LEED points, etc. Keep in mind that white EPDM costs more than normal black EPDM and doesn’t typically last as long. It also costs more than regular EPDM. (You might be better off with a TPO or PVC roof if installing a cool roof is a primary concern.)
Not a Cool Roof
Standard EPDM roof membranes are black. Standard EPDM absorbs and transmits more heat into the building than any other single-ply roof membrane. In some locations, this is actually a desirable quality, as it may help lower heating costs (rather than lowering cooling costs).
Long Service Life
EPDM roofing generally lasts significantly longer than TPO, and about the same or longer than a similarly-installed PVC roof. I have personally seen EPDM roofs last over 50 years. Of course, those roofs were consistently well-maintained and repaired as we recommended.
Lower Material Cost
Except for TPO, which will often be a little cheaper, EPDM roofing will typically cost less than any other single-ply roof system. Ballasted EPDM is the cheapest commercial low-slope roof system there is.
The cost of EPDM roofing is commonly considered one of the main benefits of the EPDM single-ply membrane roofing system.
Lower Installation Cost
EPDM is an extremely popular roofing material in colder climate zones. It’s easy to get competitive bids for an EPDM roofing installation, and just about every commercial roofing contractor in cooler regions will have roofing crews with plenty of EPDM experience.
Lower Repair Costs
Related to its low installation cost is its low repair cost. Unlike PVC and TPO, which can only be properly repaired using hot air heat welding tools (and roofers trained to use them), EPDM can be repaired using pieces of membrane and fairly cheap adhesives.
Peel-and-stick EPDM patches make minor repairs so easy that most facility maintenance technicians should be able to do it them themselves without calling a roofer. See here for how to make simple EPDM repairs.
Recycling
EPDM is one of the only flat roof materials that not only can be recycled, but actually does get recycled. See this page on the EPDM Roofing Association website for more details.
Cons of EPDM Roofing
Relatively Easily Damaged
When compared to the two other main types of single-ply membrane, TPO and PVC, unreinforced EPDM (which is used on the majority of EPDM roofs) is more susceptible to puncture damage from careless foot traffic, dropped tools, etc.
EPDM roofs should always be inspected for puncture damage after any storm where large pieces of wind-blown debris were noted.
EPDM is also easily damaged by petroleum products and kitchen grease. Restaurant kitchen exhaust and leaking or spilled HVAC lubricants are a common cause of EPDM membrane damage.
Vulnerable to Ponding Water
Unlike TPO or PVC, where the roofing sheets and flashing pieces are all heat-welded together, EPDM roofing depends on adhesives to hold everything together. These adhesives will deteriorate (very slowly!) when subjected to long-term standing water due to poor roof drainage. Poor drainage and chronic ponding water may take years off the life of an EPDM roof due to premature seam failure.
Slippery When Wet
EPDM roof membranes are extremely slippery after it rains. Anyone accessing the roof should be extremely careful when the roof is wet, and should really wait until the roof dries off before walking on it.
Appearance
A lot of people think EPDM roofs are kind of ugly. Most commercial flat roofs can’t normally be seen, so this isn’t much of a drawback, but you might want to think twice about using it for residential applications.
What is EPDM Rubber Roofing?
EPDM is a durable, waterproof, elastomeric, and highly flexible synthetic rubber which is well-suited for use as a single-ply roofing material for many reasons. “EPDM” is an acronym for “ethylene propylene diene monomer”, which is the full chemical name of EPDM rubber.
“EPDM roofing” refers to single-ply low-slope roof systems where sheets of EPDM rubber are joined together to make a waterproof roof membrane.
When people talk about “rubber” roofs, they are pretty much always talking about EPDM. EPDM is currently the only roofing material that fully qualifies as rubber that is used to construct entire roof membranes.
Although non-reinforced EPDM tends to be easily punctured (by careless foot traffic or dropped tools, for example) EPDM rubber roofing is noted for being hail-resistant, and rubber roof membranes are among the easiest to repair. Even people with no roofing experience should find it fairly easy to make simple repairs on an EPDM roof.
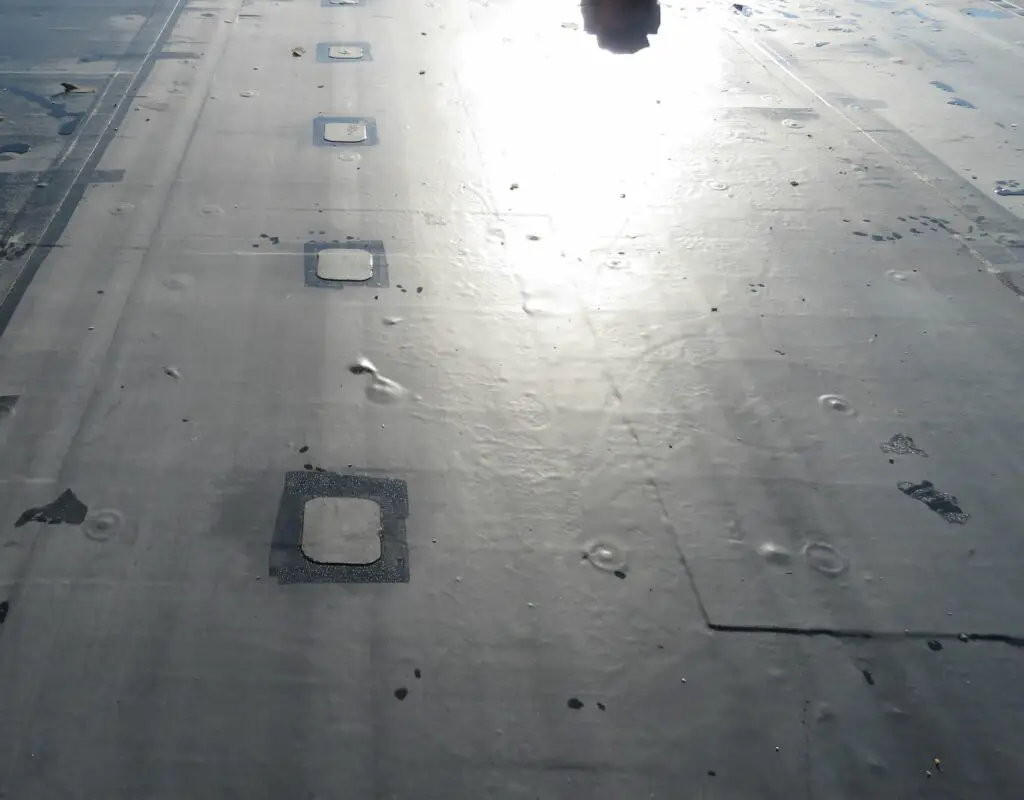
History of EPDM Roofing
EPDM was developed in the 1950’s and first used as a roofing membrane in the early 1960’s. By the 1980’s, it dominated the single-ply roofing market. It’s very common to find an older rubber roof still in place on a building today; when properly installed and well-maintained, these roofs have been known to last for over 40 years.
Currently, EPDM is used in about 20% of all low-slope (“flat”) roof installations in North America each year, including both new construction and roof replacements.
Geography of EPDM Roofing
EPDM is far more common in the north than in the south these days. Cheaper reflective white membranes such as TPO have largely replaced them in warmer climates due changing energy code and LEED requirements.
In addition, the uncured or semi-cured EPDM roofing material used for roof flashings tend to deteriorate faster under the intense UV radiation of Texas than they do in a place like Chicago, for example.
Types of EPDM Roof Systems
Single-ply roof systems are normally referred to by the way the system is attached to the building: there are ballasted systems, fully-adhered systems, and mechanically-attached systems.
Ballasted EPDM Rubber Roofing System
Ballasted EPDM roofing systems use the weight of river-washed stone (no sharp edges) or concrete pavers to hold the roof system in place. The insulation and the roof membrane are loose-laid over the roof deck, and the ballast is installed on top of the EPDM membrane.
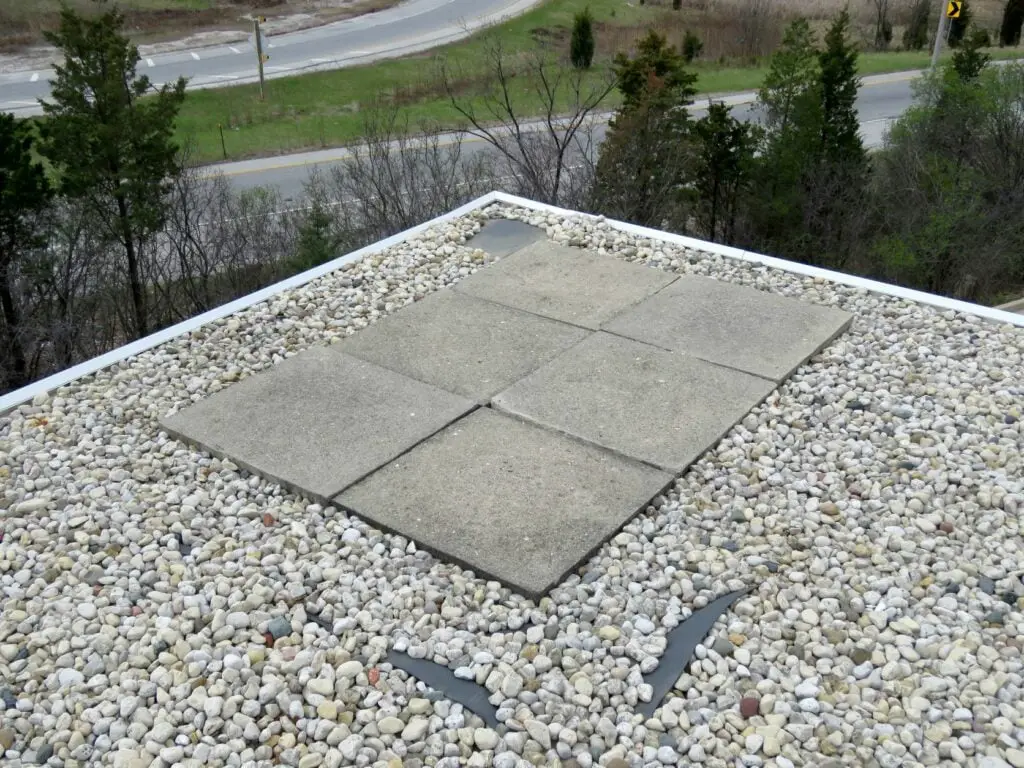
Ballasted systems do not use fasteners or adhesives to attach the roof system to the roof deck.
Ballasted systems do not normally include the hard insulation cover board that the other systems use to provide impact resistance. The ballast itself provides the impact resistance.
Because of this, ballasted EPDM roofing is far more susceptible to punctures due to foot traffic than the other systems, as the ballast stone deteriorates over time and develops sharp edges, which careless footsteps can push down into the soft insulation under the membrane.
This short video from Carlisle SynTec will help you visualize how a ballasted EPDM roof is put together:
Fully-adhered EPDM Rubber Roofing System
Fully-adhered EPDM roofing systems use adhesive to attach the entire roof membrane to the underlying insulation or insulation cover board. The insulation and cover board are typically fastened to the metal roof deck below with specialized roofing screws.
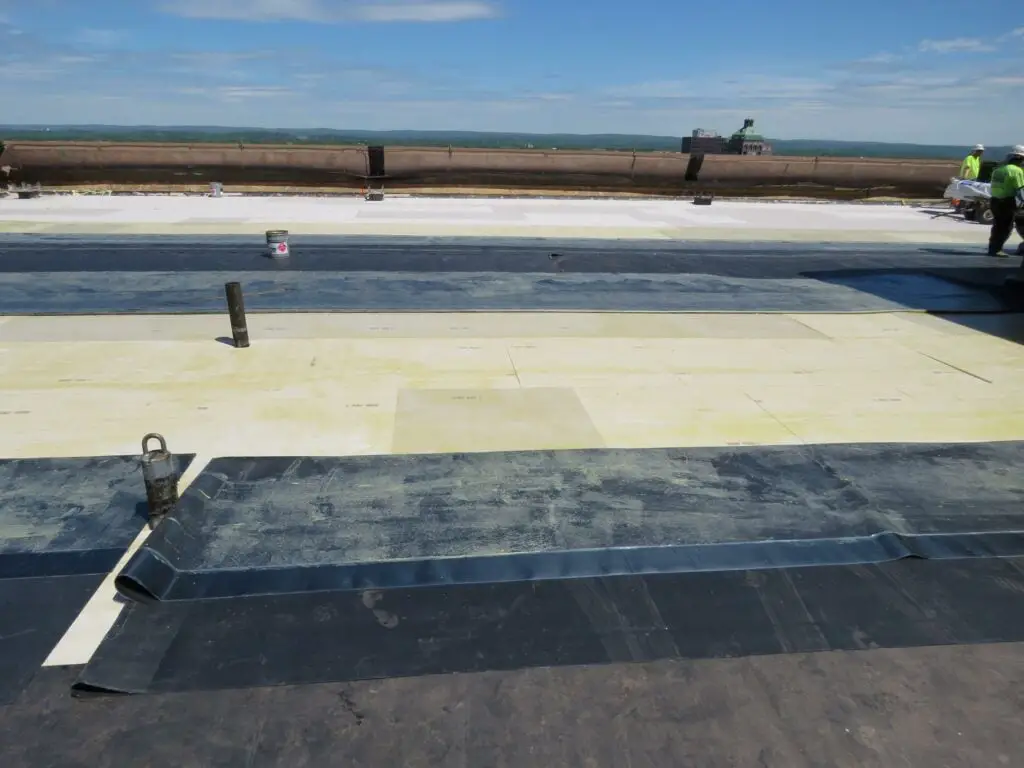
If the roof deck is structural concrete, adhesive may be used to hold all of layers of the roof system in place, instead of fasteners.
This system is called “fully-adhered” instead of simply “adhered” because all EPDM roof systems typically use some adhesive (at the field seams and at perimeter and penetration flashings).
This Carlisle video gives you a very detailed look at the process of installing a fully-adhered EPDM roof:
Mechanically-attached EPDM Rubber Roofing System
Mechanically-attached EPDM roofing systems typically use long plastic or metal batten strips to hold the field membrane in place. These battens are placed across the roof, on top of the EPDM membrane, usually at the edges of the individual sheets of EPDM that make up the field membrane.
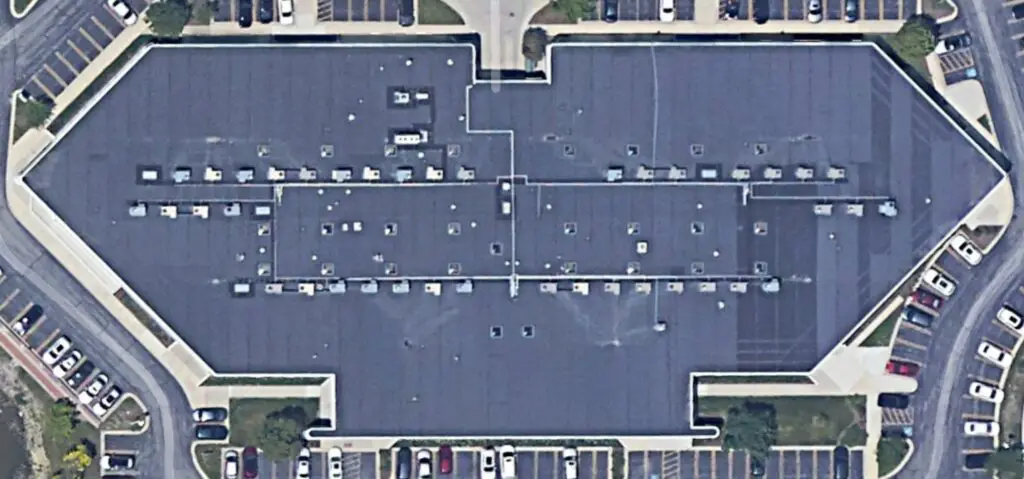
The battens come with holes for fasteners pre-drilled in them, and once they are set in place, fasteners are screwed through them, down through the roof system and into the roof deck.
The battens are covered when the seam between the two sheets is completed, the batten securing the edge of one sheet covered by the seam edge of the EPDM sheet next to it.
Some mechanically-fastened EPDM roofs don’t use battens, and will simply have the fasteners (long, heavy screws) installed with fastener plates in the manner described above, minus the battens.
Here’s another short video from Carlisle that shows how a mechanically-attached EPDM roof is constructed:
Size of the EPDM Membrane Sheets
Individual sheets of EPDM rubber come in a variety of widths and lengths, with 10 ft. x 100 ft. being a typical size for large roof installations.
Much smaller pieces intended for use as membrane patches or for smaller residential flat roofs are easy to find on Amazon.
Standard membrane thicknesses are 45-mil (0.045 inches or 1.14 mm), 60-mil, and 90-mil for unreinforced EPDM, and 45-mil, 60-mil, and 75-mil for EPDM reinforced with polyester scrim.
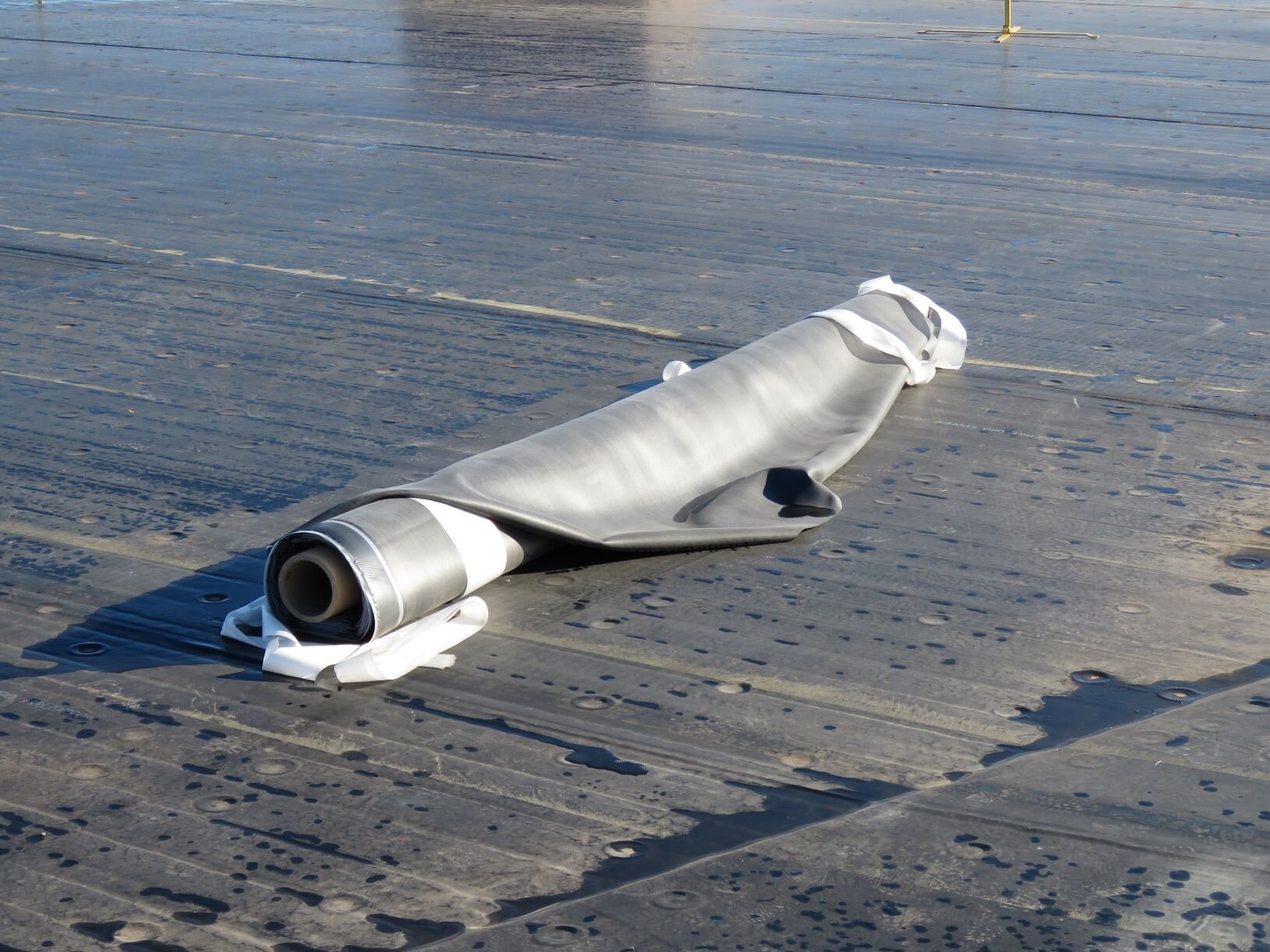
Chemical Composition of EPDM Rubber
EPDM is a synthetic rubber, ethylene propylene diene monomer (also called “ethylene propylene diene terpolymer” because it’s a polymer made from three monomers). The rubber used in roofing contains roughly 40% actual EPDM (EPDM base resin).
The other ingredients typically include carbon black (around 25%), plasticizing and extending oils (around 20%), with the remainder being various additives including anti-oxidants, anti-ozonants, fire retardants, curing agents, and inert fillers.
Reinforced EPDM vs Non-Reinforced EPDM
Most EPDM roofs in place today use unreinforced sheets, but membranes manufactured with a polyester reinforcing scrim are also used where recommended or required, particularly in mechanically-attached systems.
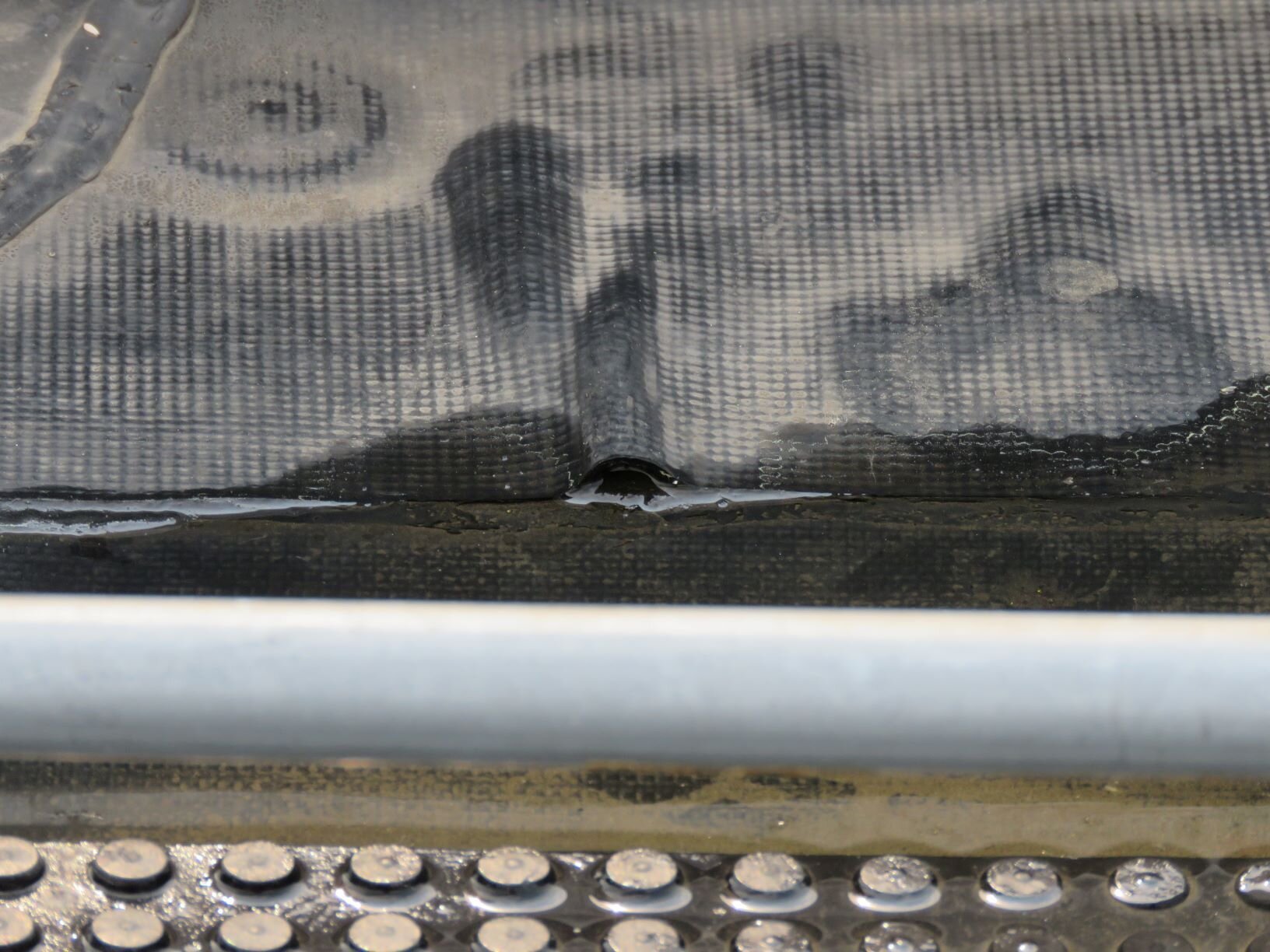
Parts of an EPDM Roof System
Common components in this type of roof assembly are: the roof deck, an air or vapor barrier (if needed), one or more layers of insulation, a cover board (if needed), and the membrane itself, along with attachment components such as adhesives, fasteners, or ballast.
The field membrane (the vast majority of the surface of the roof) is formed from large sheets (typically 10 feet by 100 feet) of fully-cured EPDM rubber, seamed together with adhesives or adhesive tape during the roof installation.
Smaller pieces of fully-cured or semi-cured material are used to form the flashings at the perimeter of the roof and at HVAC curbs and other penetrations through the roof. Uncured material is sometimes used on the corners of curbs or other locations with sharp angles.
Characteristics of EPDM Membranes
EPDM is an elastomeric, thermoset, black or white synthetic rubber noted for its durability. It has good resistance to moisture, UV rays, heat, hail, ozone, and alkalis and acids. It has a high tensile strength, resists tearing, and remains flexible in cold weather (down to -45°F/-43°C).
EPDM Roofing Colors
Black EPDM Membranes
Sheets of EPDM are black because carbon black is added to them during the manufacturing process. As a raw material, carbon black is an extremely fine black powder, almost pure carbon, which is refined from petroleum or coal. It makes up about a quarter of the final product.
The addition of carbon black strengthens the EPDM resin, reinforcing its molecular structure and increasing its tensile strength. It also protects the polymeric chemical bonds of the material by blocking harmful UV rays, which is a critical function, and largely responsible for the excellent lifespan of rubber field membranes.
Because almost all EPDM roofs are black, they rarely qualify as “cool roofing” unless coated with a reflective roof coating. The black membrane absorbs almost all of the heat from the sun’s rays during the day, and these roofs can reach temperatures of over 180 degrees on a hot afternoon. In warmer areas where cooling degree days outnumber heating degree days, black EPDM has generally been replaced as a single-ply roofing material by white PVC and TPO.
On the other hand, in colder climates where heating degree days outnumber cooling degree days, a black roof membrane can actually reduce annual energy costs versus white roofing membranes.
White EPDM Membranes
White EPDM is also available and can be used where a cool roof is called for.
White EPDM is formulated with a white pigment, typically titanium dioxide, in place of carbon black. Titanium dioxide is less UV resistant than carbon black, and as a result the white version of this roofing material tends to be somewhat less durable than the black.
White rubber roofs are uncommon; it’s more expensive than other white roofing materials and their share of the cool roof market is dwarfed by that of PVC and especially TPO. White EPDM is also more expensive than the regular black.
For a good article on white EPDM, see here.
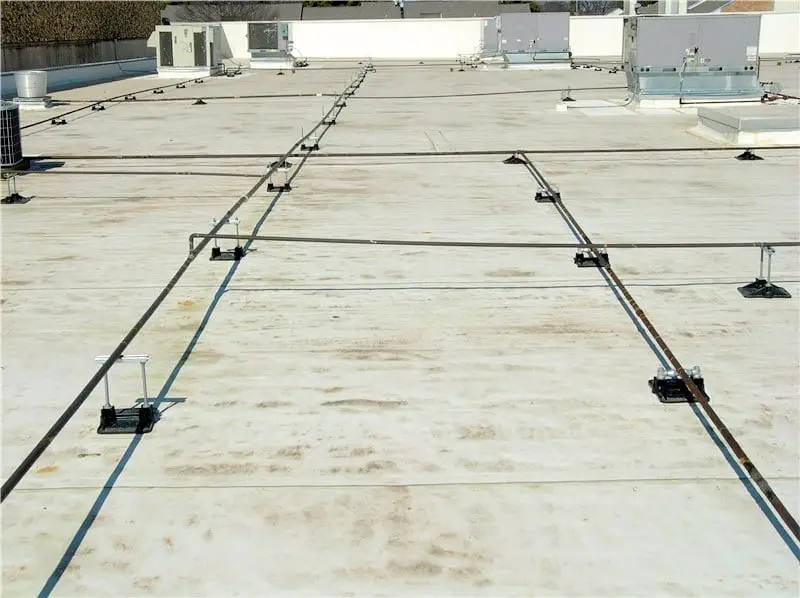
EPDM is Elastomeric
“Elastomeric” refers to the ability of a material to stretch and return to its original dimensions without being damaged.
When new, the unreinforced roofing material normally used in ballasted or fully-adhered systems can typically stretch more than three times (300%) its original size without breaking, although this may be reduced somewhat as the membrane ages.
The reinforced EPDM normally used in mechanically-attached systems is constrained by the reinforcing polyester scrim, which reduces the elasticity of the roof membrane as a whole, and can only stretch about 35% before breaking.
For comparison, PVC roof membranes can only stretch about 15% before breaking, TPO membranes 27%, and an asphalt built-up roof about 2%.
EPDM is Thermoset
“Thermoset” means that after the polymer chains are cross-linked using heat and chemical curing agents during the manufacturing process, new molecular cross-links cannot be formed. The material is now heat-stable and any future application of heat will either have no effect on it or will simply damage it (at very high temperatures).
In other words, after it’s manufactured, you can’t use a hot air welder on it. This is why adhesives or adhesive tape is required to join pieces of EPDM roofing together. (Thermoplastic roof membranes such as PVC or TPO, on the other hand, are always able be welded or otherwise altered using (very) hot air.)
Cured and Uncured Material
The completely chemically cross-linked material used as a field membrane is also called “fully cured EPDM“.
Semi-cured and uncured EPDM roofing products are often used as a flashing material where the roof makes an angle change at walls, curbs, or roof penetrations such as vent stacks. These forms of the material are manufactured by not allowing the EPDM polymer chains to become fully cross-linked.
This allows those materials to more easily conform to angles after installation without trying to snap back into a flat sheet shape like the fully cured EPDM roofing product does.
It also means that these materials are more vulnerable to UV radiation and heat, and they will deteriorate faster than the rest of the roof. Deteriorated flashings are a common culprit when it comes to roof leaks in older roofs, particularly the corner patches at curbed HVAC units.
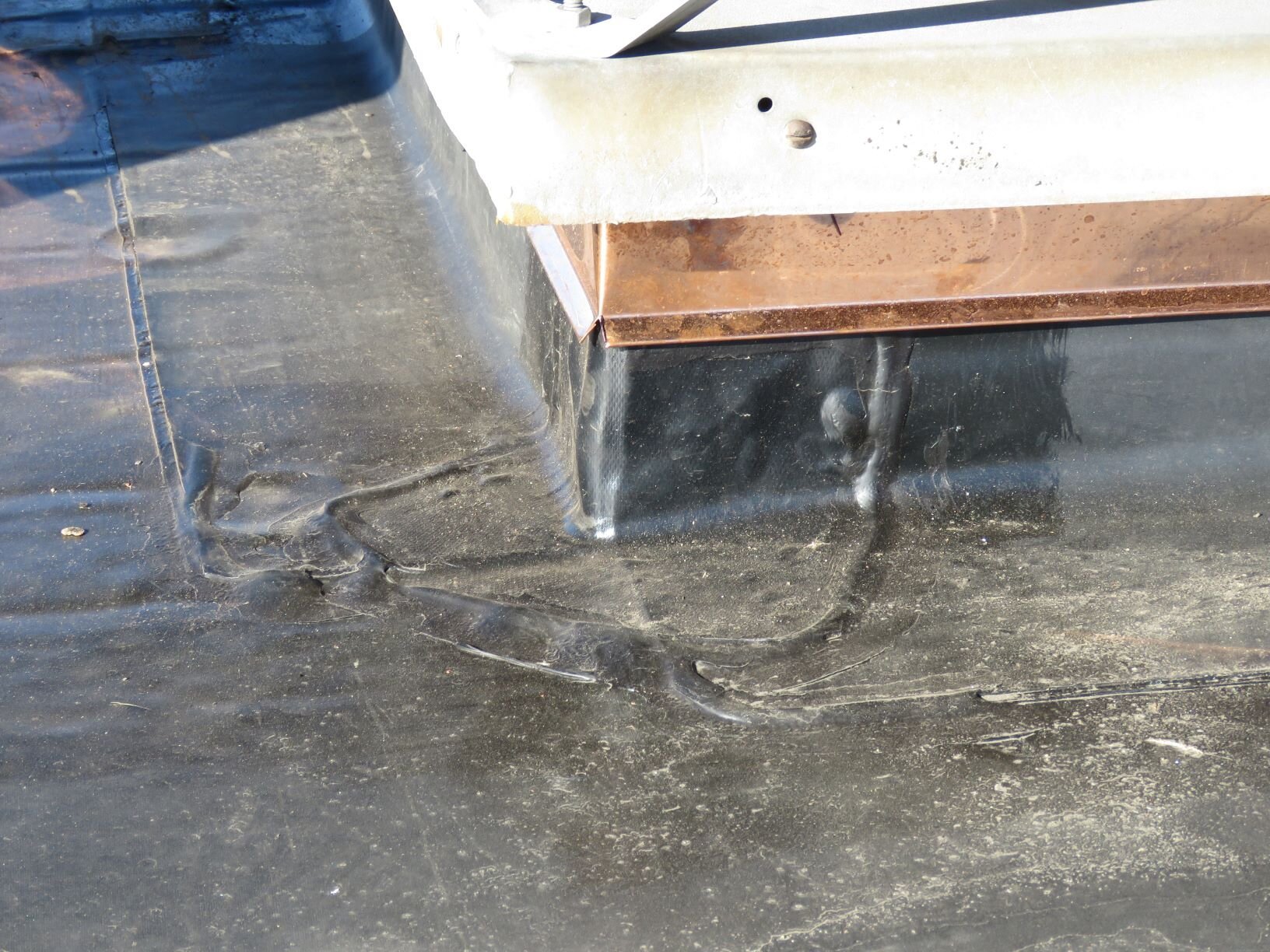
Durability
Fully-cured EPDM is one of the most durable low-slope roofing materials available.
Due to its molecular stability, its exceptional resistance to UV radiation, and its non-reactivity in the presence of corrosive environmental substances such as water, acids, and ozone, the sheets that make up a roof’s field membrane can remain functional for over 50 years.
When a rubber roof reaches the end of its service life, it’s almost always due to the failure of the adhesive in the seams or a part of the roof system other than the field membrane material, which tends to be the last to go.
Lifespans of EPDM Rubber Roof Systems
If an EPDM rubber roof has been installed correctly, with high-quality workmanship and high-quality materials, the key determining factor in the length of the expected useful service life of the roof will be the thickness of the membrane material. The second most relevant factor is the method of attachment.
The thicker the EPDM roofing membrane, the longer the system will last.
Fully-adhered membranes generally last longer than mechanically-attached membranes, which generally last longer than ballasted membranes.
The longest lasting type of EPDM roofing will normally be a 90-mil fully-adhered roof, which will typically last around 35 years.
The type with the shortest lifespan will normally be a 45-mil ballasted roof, which will typically last around 15 years.
See our chart showing the life expectancies of all kinds of roofing systems for a more detailed breakdown of the lifespans of the different systems, as well as the lengths of typical warranties.
These are general guidelines and any kind of roof can fail much earlier than its design lifespan if it is poorly maintained, subjected to damaging chemicals or foot traffic, improper alterations, or extreme weather events beyond what the roof is designed to handle.
Things That Damage EPDM Rubber Roof Membranes
Rubber roof membranes are easily damaged by sharp objects, oils, gasoline and other fuels, grease, fats, and solvent-based asphalt compounds such as asphalt roof cement. See this chart for a long list of chemicals and whether you can expect them to damage EPDM.
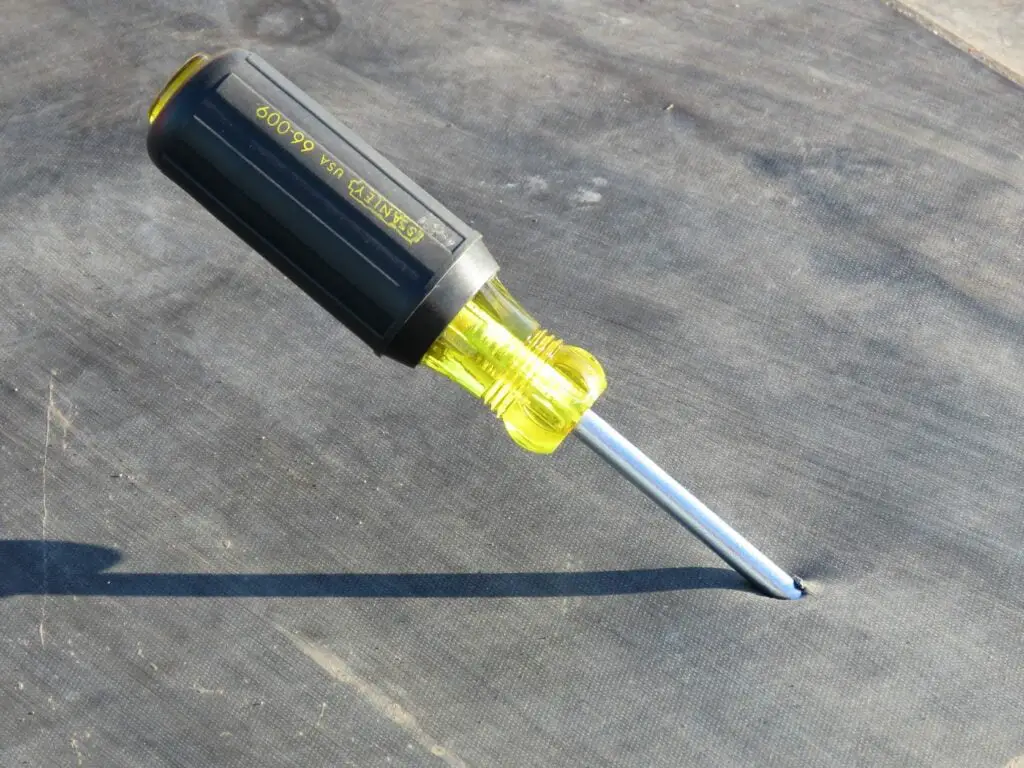
Sharp Objects
EPDM rubber roof membranes, especially unreinforced membranes, are fairly easy to puncture.
Dropped tools, nails or screws which are spilled on the roof and then stepped on, and even sharp stones caught in the tread of a boot have all been known to make holes. This is a common source of roof leaks with this type of roof.
Special care should be taken when walking on older ballasted EPDM roofing systems, as the ballast stone tends to crack and split over time due to thermal cycling. There are usually a large number of jagged stones all over a ballasted roof that you want to avoid stepping on with too much force. Tread lightly!
Fasteners Backing Out
Fully-adhered EPDM systems may be damaged if the fasteners that secure the cover board and insulation underneath the membrane become loose and start working their way back out of their holes. This can be the result of poor installation, corrosion of the deck or the fasteners themselves, or water damage to the cover board or insulation due to roof leaks.
These fasteners can back out and up, puncturing the membrane from below. Luckily, this is an easy issue to spot during a maintenance inspection, and can be easily dealt with (for roofs with, say, less than 10 years of service life remaining) simply by applying a thick patch over the problem location.
A proper repair for a roof that still has more than 10 years of service life left would be to cut the membrane around the area, pull out and replace the fastener, and patch the area.
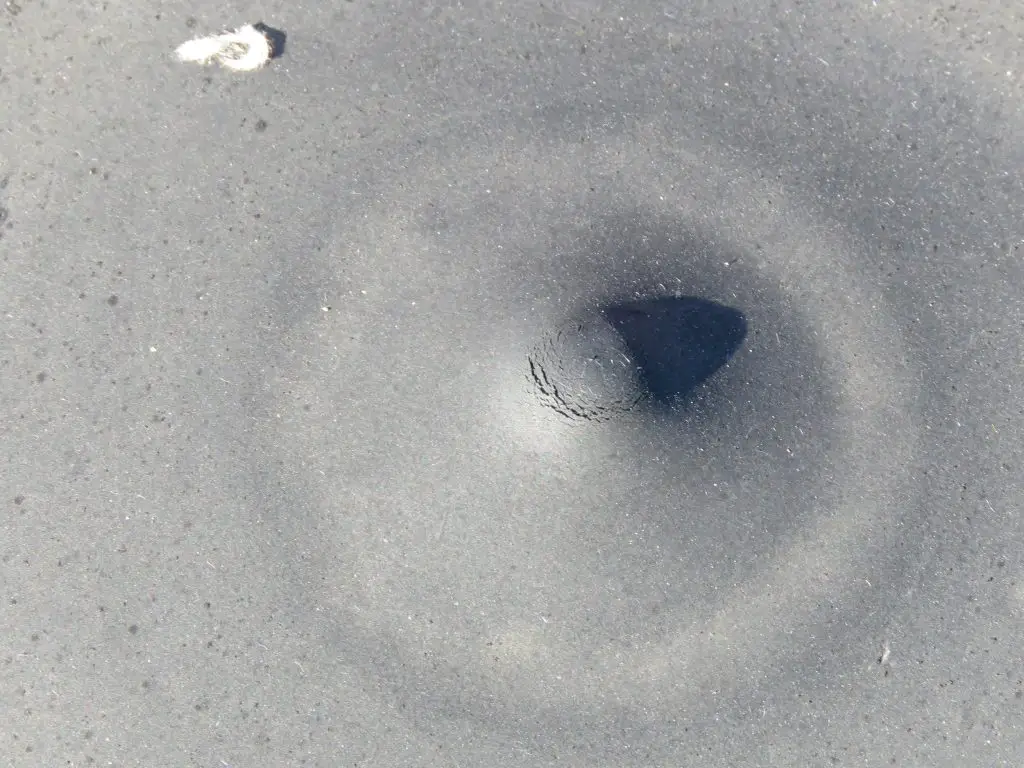
Compatibility with Asphalt
EPDM roofing is not generally compatible with asphalt, although temporary contact with pure asphalt or polymer-modified asphalt is not something to worry about. However, EPDM is completely incompatible with solvent-based asphaltic roofing materials such as roofing cement or roofing mastic.
These materials combine petroleum-derived solvents with asphalt to produce a workable, plastic asphalt that can be spread with a trowel or applied with a caulking gun. The solvents in these products will quickly damage EPDM roofing membranes.
Although EPDM can tolerate some forms of asphalt quite well in some cases, to be safe you should never use an asphalt-based product on an EPDM roof.
Other Petroleum Products
Occasionally, other trades (we’re looking at you, HVAC mechanics) will spill petroleum-based fluids on a roof and fail to immediately and completely clean it up.
Within weeks a contaminated EPDM roofing membrane will wrinkle and start to break down; the material at the location of the spill will grow thinner and weaker, and eventually small holes will appear.
It’s a good idea to check the area where anyone has been working up on your roof as soon as they finish, in case you need to have them do a better job cleaning up
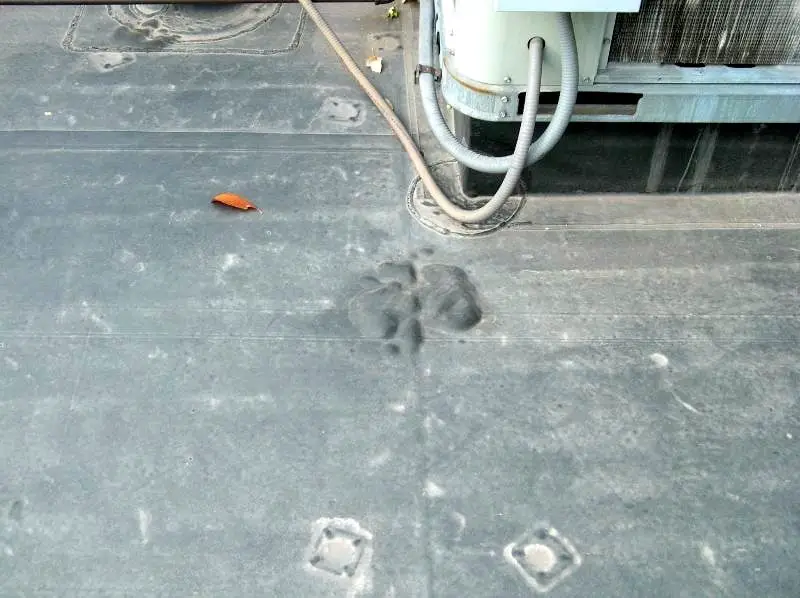
Restaurant Kitchen Grease
A major concern with EPDM roofing is restaurant kitchen exhaust. It’s very common to see severe roof damage around kitchen exhaust fans as kitchen grease accumulates on the surface of the roof. Kitchen grease affects EPDM roofing much the same way that petroleum products do.
Damage to the roof can be prevented by installing a protective layer of a more grease-resistant roofing material (sheets of PVC roof membrane work well) around the exhaust location. This must be coupled with a good rooftop grease containment system.
Both of these things should be professionally installed, and they must be installed before the damage starts. EPDM roofing already damaged by grease will have to be removed and replaced. It should not be left in place and simply covered up by a patch, as the patch may also become contaminated.
Property managers should keep a close eye on their restaurant tenants. Restaurants seem to remodel their spaces more often than the average tenant, and they tend to make more unauthorized roof penetrations.
If a new tenant is opening a restaurant, whether or not the space has been used as a restaurant before, that is a particularly good time to inspect the roof. Have someone check to make sure they aren’t making unauthorized roof penetrations. Make certain that they’ve installed adequate protection for the roof around the new kitchen exhaust vents.
About the Author
Jack Gray is a principal roof consultant and vice president at the Moriarty Corporation, an award-winning building enclosure consultant firm founded in 1967. He is also the editor of the Roof Online website.
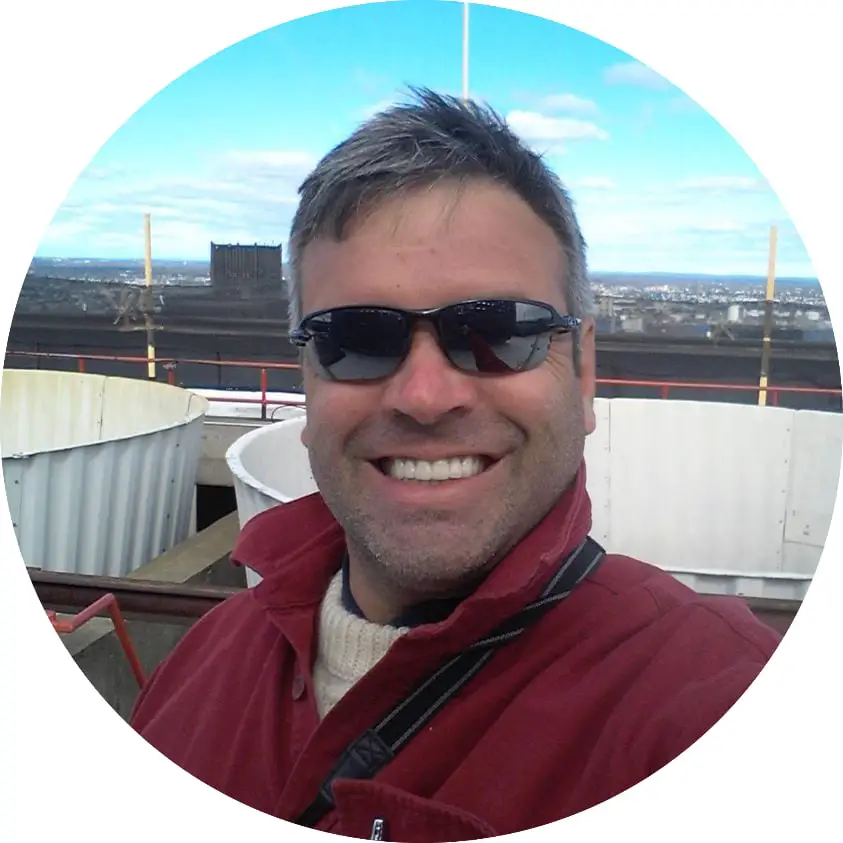
Mr. Gray has worked in the roofing industry for over 25 years, with training and practical experience in roof installation, roof inspection, roof safety, roof condition assessment, construction estimating, roof design & specification, quality assurance, roof maintenance & repair, and roof asset management.
He was awarded the Registered Roof Observer (RRO) professional credential in 2009.
He also served as an infantry paratrooper in the 82nd Airborne Division and has a B.A. from Cornell University. Read full bio.
Related Articles
External Sources & References for EPDM Roofing Information
1. Book Recommendation: Manual of Low-Slope Roof Systems: Fourth Edition by C.W. Griffin & Richard Fricklas
2. General: See this in-depth general article about various roof systems on the Whole Building Design Guide site, which is maintained by the National Institute of Building Sciences.
3. General: For a decent general discussion of EPDM as a material, see the Wikipedia EPDM page. Not much information specific to EPDM roofing, though.
4. General: The EPDM Roofing Association has thorough and accurate information at this location (see the menu on the left side of the page for particular aspects of EPDM roofs). Just remember that this is an industry association that was formed with the purpose of providing “data documenting the many benefits of EPDM roofing systems” (quoted from their website).
5. General: Industry news can be found on the EPDM Roofing Association website.
6. Building Codes: “R905.12 Thermoset Single-Ply Roofing” from the 2021 International Residential Code and “1507.12 Thermoset Single-Ply Roofing” from the 2018 International Building Code. Both available on the UpCodes website.
7. Chemical Compatibility of EPDM: See this chart for a long list of chemicals and whether you can expect them to damage EPDM. Note that EPDM roof seam adhesive and semi-cured or uncured EPDM flashings may be affected differently than fully-cured EPDM field material. Chart is made available by Mykin Inc.
8. Hail Damage: “Comparative Performance of EPDM Rubber Roofing Membrane as Protection against Hail Damage” is worth a look. Good pictures; also pictures of hail damage to other roof types, not just EPDM. Available on the EPDM Roofing Association website.
9. Inspection of rubber roof systems: ROOFER: Membrane and Flashing Condition Indexes for Single-Ply Membrane Roofs – Inspection and Distress Manual is an extremely detailed and valuable resource put together by the US Army Corps of Engineers’ Engineer Research and Development Center. Available for download at the Defense Technical Information Center website.
10. Repair of EPDM Seams: See this article, Technical Details: Proper Installation and Repair of EPDM Seams, on the Roofing Contractor magazine website.
11. Safety: See this material safety data sheet for health and safety information about EPDM at the Carlisle Syntec website. This is only an example and other products and brands may be different.
12. Technical: EPDM Roof Construction Details: An extensive list of easy-to-view details is provided on the GenFlex website.
13. Technical: See this product data sheet for the technical characteristics of EPDM roofing at the Johns Manville website. This is only an example and other products and brands may be different.
14. Technical: Ballasted EPDM, what is it? See this page on the Carlisle Syntec website.
15. Technical: See Carlisle’s Fully-Adhered EPDM page.
16. Technical: See Carlisle’s Mechanically-Attached EPDM.