Built-Up Roofing (BUR): What It Is, Types, Issues & More
By Jack Gray, Roof Online Editor • Last updated August 18, 2024
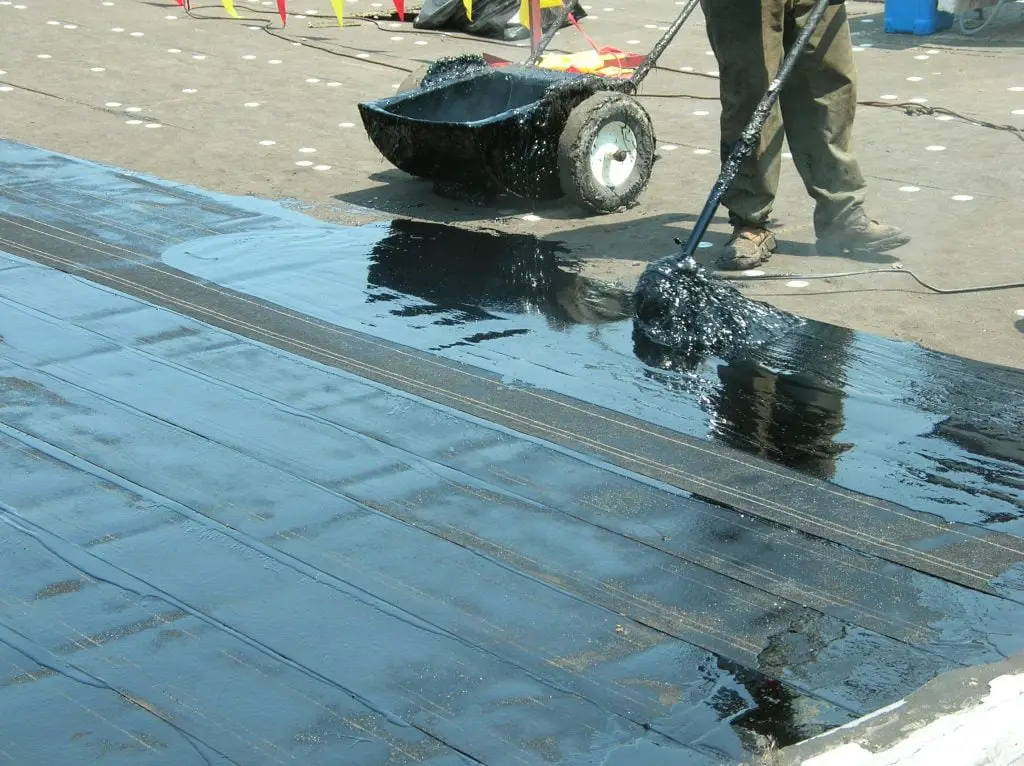
Table of Contents
What is a Built-up Roof?
A built-up roof is a type of “flat” or low-sloped roof made up of multiple layers of bitumen (asphalt or coal tar pitch) and reinforcing felts.
ASTM International, in ASTM D1079-20 (Standard Terminology Relating to Roofing and Waterproofing) defines built-up roofing like this: “Built-up Roofing, n—a continuous, semiflexible membrane consisting of plies of saturated felts, coated felts, fabrics or mats assembled in place with alternate layers of bitumen, and surfaced with mineral aggregate, bituminous materials, or a granule surfaced sheet (abbreviation, BUR).”
Typical built-up roofs have three to five layers, called “plies”. Built-up roof systems typically have a layer of insulation under the waterproof bitumen membrane, as well as some sort of protective surfacing, most commonly gravel.
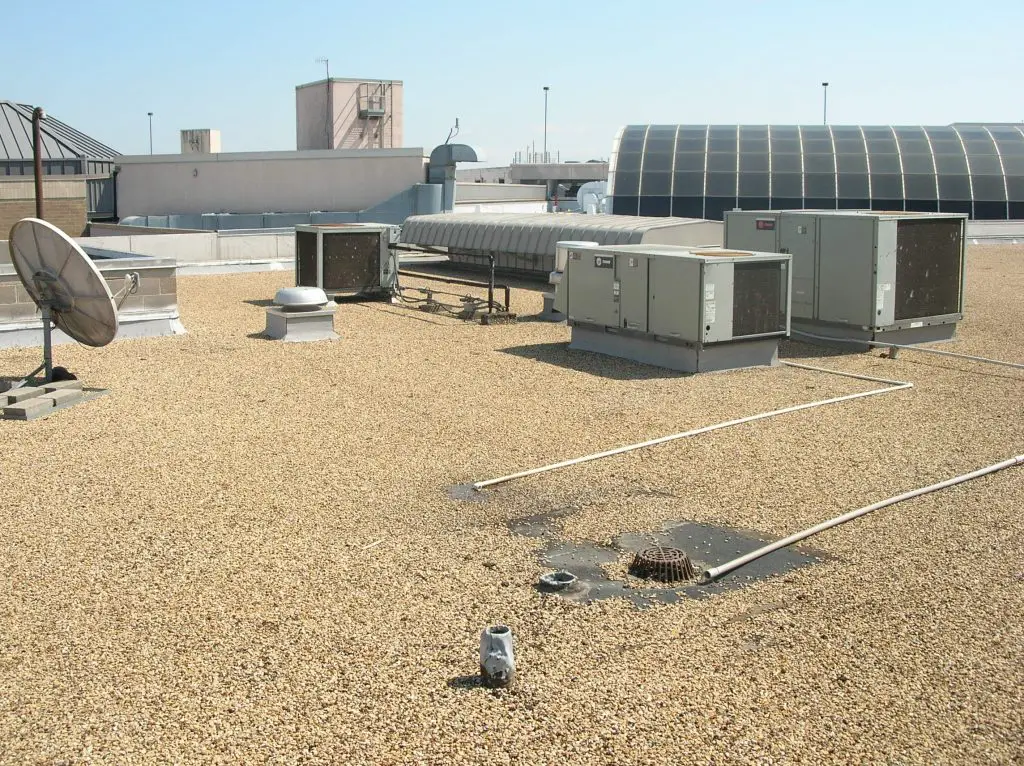
Other protective surfaces for built-up roofs include reflective roof coatings, asphalt emulsion coatings, sheets of modified bitumen, or some combination of these. When gravel is used, it usually adds about 3 to 4 pounds in weight per square foot to the roof system.
A built-up roof is typically called a “BUR” roof in technical literature. The colloquial term “tar and gravel roof” refers to built-up roofs.
BUR systems have been used in the U.S. since the 1850s, and bituminous materials such as asphalt and pitch have been used to weatherproof structures for thousands of years. For a century, up until around 1980, the vast majority of all commercial low-slope roofs in the United States were built-up roofs. Due to the introduction and wide-spread adoption of single-ply roofing systems in the second half of the 20th century (the 1960’s through the 1990s, depending on the single-ply material), along with rising crude oil prices, the share of new roof installations that use BUR fell to less than 2% by the 2020s.
Many, many, many existing built-up roofs are still in use, however; they will be around for a while yet, and they still need repairs, maintenance, and people who understand how they are put together. Many more original built-up roofs are still in place on buildings, but hidden by the single-ply systems that were installed on top of them – these will all have to be removed the next time the next time those roofs need to be replaced.
Components and Materials in BUR Assemblies
- Roof Deck: The foundation for any roofing system is the deck, which significantly affects the performance of the roofing system. The type of deck used depends on the building’s design and purpose. Steel decking is the most common material you’ll find under a BUR, but structural concrete and poured gypsum are not unusual, and I’ve personally seen more than one wood plank deck supporting a BUR system. A roof deck must simply be able support the roofing system properly. The deck is the only part of a roof assembly that is considered to be structural.
- Vapor Barrier: Vapor barriers are often recommended or even required in order to prevent interior moisture from migrating into the roof system, where it can saturate the above-deck insulation. Vapor barriers reduce the risk of premature roofing failures by reducing condensation within the roof system, which can degrade insulation, fasteners, and base plies.
- Thermal Insulation: Roof insulation helps conserve energy but must be properly selected and installed to avoid potential problems. Improper insulation can lead to issues such as condensation and energy inefficiency. The thickness of the insulation layer within a roof system is typically determined by the roof R-value requirements dictated by the energy code that was in effect when the roof was installed.
- Base Sheet: The base sheet is a layer of specialized roofing felt that serves as the bottom-most layer of the roof membrane. Typically secured with fasteners and fastener plates that pass through the insulation to the roof deck, the base sheet anchors the BUR membrane to the building. The felt used for the base sheet is sold as a separate product than the ply felts; the base sheet felt is stronger.
- Roof Membrane: The waterproof membrane is the most important component of any low-slope roofing system. A built-up roof membrane consist of roofing bitumen (asphalt or coal tar pitch) and reinforcement felts, which strengthen the bitumen and allow the otherwise brittle (asphalt) or soft (coal tar pitch) roof membrane to resist stresses caused by building movement and thermal expansion and contraction. Roofing felts come in various types, such as asphalt or coal tar saturated organic or fiberglass felts, and (occasionally) nonwoven polyester. Specific felts are recommended for different bitumen types, and it’s essential to follow the manufacturer’s guidelines when selecting materials. Built-up roof membranes tend to be about half an inch thick and weigh around 2.5 pounds per square foot (this does not include the gravel surfacing).
- Flashing Components: “Roof flashing” is a term that refers to the roof components that are used to create weather-tight seals where the roof membrane is penetrated (by conduit lines or vents, for instance) or interrupted by features like parapet walls, HVAC unit curbs, or drains. Proper flashing design and installation will help prevent a large number of common roofing problems. Pieces of modified bitumen roofing are often used for the flashing elements on a built-up roof.
- Protective Surface: The most common surfacing materials used in BUR systems (gravel, slag, or other mineral aggregates) protect the roof membrane against UV radiation, fire, and physical damage from foot traffic and hail. During the last stage of a built-up roof installation, mineral aggregates such as gravel are embedded in an extra-thick surface layer of bitumen called a “flood coat”. Gravel also helps to secure the roof, preventing wind uplift damage to the roof membrane simply by virtue of its weight. Other surfacing materials include rolls of mineral granule surfaced modified bitumen and various types of coatings (coatings will typically only protect against UV damage). Aluminum roof coatings are often applied to the membrane to improve reflectivity and create a “cool roof” effect. Coatings must be appropriate for the roof slope and follow manufacturer specifications.
- Bitumen as a Critical Element: Bitumen (most often asphalt, but also coal tar pitch) is the primary element of a BUR system, providing waterproofing as well as holding the entire system together. The bitumen forms a fused membrane that resists building movement and thermal changes. Both asphalt and coal tar bitumen are thermoplastic, meaning they become fluid with heat and solidify as they cool.
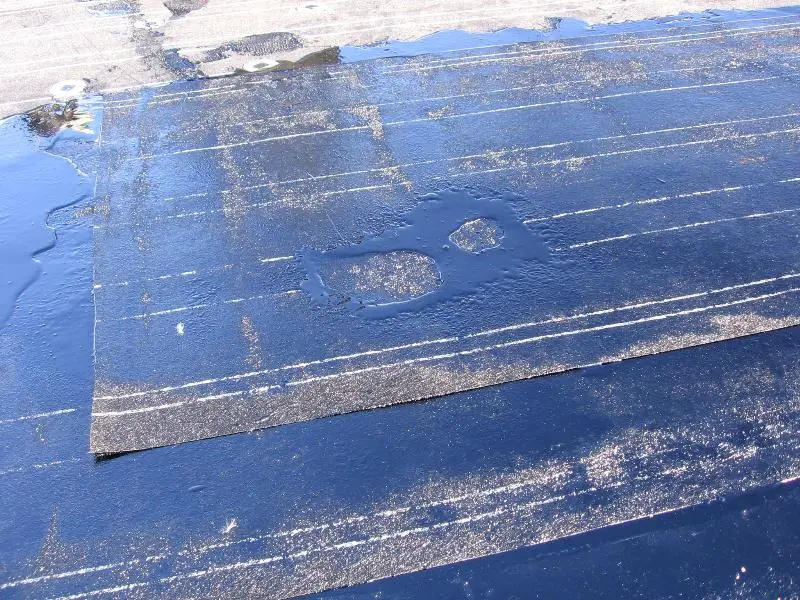
Bitumen Types, Selection, and Quality
- Asphalt Quality: Asphalt used in BUR systems is obtained from petroleum crude oil. The refining process can vary depending on the source, leading to varying asphalt qualities. The use of high-quality asphalt is very important for the long-term performance of built-up roofing membranes.
- Coal Tar Pitch: Coal tar pitch, derived from coal, was used in the majority of BUR systems for over a hundred years, but it has been almost entirely replaced by asphalt since the 80s. Due to the fact that it always retains the characteristics of a fluid, if even just ever-so-slightly, coal tar pitch has a unique self-healing ability, allowing it to slowly mend small cracks and fractures. It also has unique health advisories issued by OSHA, which complicates the use of coal tar pitch these days (although it’s still an excellent roofing material).
- Selecting Bitumen for BUR: The correct bitumen must be selected based on the roof’s design, slope, environmental factors such as anticipated ponding water, and sometimes the part of the roof it’s being used for. BUR involves a fusion process, where heated bitumen bonds with roofing felts to create a monolithic mass. Correct application temperatures are also vital for a quality roof membrane system. Bitumen that is overheated in the kettle before application tends to become brittle afterwards, resulting in a roof membrane that cannot properly resist the environmental stresses a roof is subject to.
- Asphalt: Asphalt is classified into four types based on its softening point and susceptibility to flow at ambient roof temperatures. Each type has specific applications, and asphalt must be heated to a precise temperature (both during manufacture and during application) for proper bonding and performance.
- Dead-Level Asphalt: A roofing asphalt conforming to the requirements of ASTM Specification D 312, Type I. This asphalt is for use in roofs which do not exceed a ¼ in 12 slope (2% slope).
- Flat Asphalt: A roofing asphalt conforming to the requirements of ASTM Specification D 312, Type II. This asphalt is for use in roofs which do not exceed a ½ in 12 slope (4% slope).
- Steep Asphalt: A roofing asphalt conforming to the requirements of ASTM Specification D 312, Type III. This asphalt is for use in roofs which do not exceed a 3 in 12 slope (25% slope).
- Special Steep Asphalt: A roofing asphalt conforming to the requirements of ASTM Specification D 312, Type IV. This asphalt is for use in roofs which do not exceed a 6 in 12 slope (50% slope).
- Coal-Tar Pitch: Generally, only one type of coal tar pitch is used for roofing. As with asphalt, the pitch must be heated to the correct temperature (both during manufacture and application) for optimal performance. Note that coal tar pitch is not recommended for roofs with a slope greater than ½-in-12 (4% slope), due to its fluid nature.
Application Techniques
- Felts and Vapor Retarders: There are different types of felts and vapor retarders used in BUR systems, including organic base sheets, glass fiber sheets, and polyester sheets. Each type has distinct properties and is used for specific purposes in roofing systems.
- Surfacing Materials: BUR systems can be surfaced with materials such as mineral cap sheets, mineral aggregate, asphalt coatings, or aluminum roof coatings. These materials protect the membrane from sunlight and weather damage and provide additional benefits like fire resistance.
- Hot-Applied BUR: In hot-applied BUR systems, roofing felts are embedded in hot bitumen, applied by mopping or machine spreaders. Proper application techniques must be strictly followed to ensure full coverage and proper bonding of the felts to the bitumen. It’s important to make sure that the bitumen is not overheated prior to application, and it’s important that the bitumen is not allowed to cool down too much before it’s applied to the roof. (As an example, type III asphalt should not be heated to over 500°F in the kettle, and should not be applied to the roof at a temperature below 450°F.)
- Cold-Applied BUR Systems: Cold-applied BUR systems use “cold process” adhesives instead of hot bitumen. These systems offer advantages like safer installation and less labor-intensive processes. However, they also have limitations, such as increased weather restrictions and relatively lengthy curing times.
- Application of Cold-Applied BUR: The application of cold-applied systems follows a similar process to hot-applied systems but uses adhesives applied by spray, brush, or squeegee. Pre-cutting and relaxing glass felts help prevent issues like ridging in the finished roof.
Common Problems in BUR Systems
Blisters
Blisters are a common problem in BUR systems and are caused by voids, or unbonded areas, between layers of the membrane. They can range in size from small spots to large humps and may shorten the roof’s service life if not repaired. You should never step on a roof blister; the roof membrane is very easy to puncture or otherwise damage at blister locations.
Blister Mechanics and Prevention: Voids in the interply bitumen mopping application or at the insulation-membrane interface are very likely to result in blister formation. These voids may be caused by moisture in the felts, improper mopping techniques, air entrapped during application, or warped insulation boards. Blisters grow larger over time as the air and water vapor inside of the blister expands and contracts during daily thermal cycles, forcing the part of the membrane that contains the blister to get tighter and looser in turns.
Effect of Temperature on Blisters: The initial mechanism of blister grow the is the creation of water vapor from trapped liquid water (trace amounts of moisture contained within the layers of the membrane). As trapped moisture expands into vapor when the membrane is heated by sunlight, its volume increases by up to 1,600 times, depending on temperature and pressure levels. Very little moisture can create a very large blister. And as temperatures rise (and a dark-surfaced roof can be around 180 degrees during a hot afternoon), the rise in temperature causes a significant increase in pressure within the void, leading to blister growth.
Role of Coated Felts in Blistering: The use of coated felts instead of saturated felts can exacerbate blistering issues. Coated felts are stiffer and harder to fully bond to the bitumen layers, making them more likely to contain voids. The lack of perforation or “breathability” in coated felts prevents the escape of air or moisture during application, further contributing to blister formation.
Urethane Boards and Blistering: Urethane insulation boards are prone to promoting blistering due to their low thermal conductivity and heat capacity. When hot bitumen is applied to urethane boards, the sudden rise in temperature creates vapor pressure that leads to bubbles or channel voids in the asphalt.
Membrane Splitting
Splitting is the second most frequent roofing issue after blistering, and it is the most serious. Splitting tends to occur in colder climates and is more common on larger roof areas with widely spaced contraction-expansion joints. These splits typically form parallel to the longitudinal direction of the felts due to differences in thermal contraction and material strength between the transverse and longitudinal directions.
Causes of Splitting: Several factors contribute to membrane splitting, including thermal contraction, movement within insulation, moisture absorption by felts, and shrinkage due to drying. Asphalt also becomes more brittle as it ages; the older an asphalt BUR is, the more likely it will experience splitting. Very old built-up roofs may experience catastrophic splits which can result in, basically, holes in the roof that are over a hundred feet long. If a built-up roof is starting to experience frequent, multiple cases of splitting, that’s a sign that the roof has reached the end of its useful service life and needs to be replaced soon.
Ridging & Fishmouths
Ridging occurs when ridges or wrinkles form in the roofing membrane, typically above insulation joints. This issue arises when the membrane does not have enough flexibility to accommodate movements in the underlying substrate. Fishmouths are small openings in the membrane where a ridge or wrinkle meets the edge of a felt and makes it stick out above the bitumen surface of the roof.
A big problem with any exposed felts at the surface of a BUR is that they can absorb water and allow it to seep deeper into the membrane. Fishmouths are doubly bad because in addition to water being absorbed by the exposed felts, they provide a direct path for water to follow and find further susceptible locations inside the membrane. Liquid water may also sit inside of ridges that end with an open fishmouth until it freezes in the winter, with this ice splitting the membrane as it expands.
Slippage
Slippage happens when the membrane shifts out of place, usually because of poor adhesion or insufficient attachment of the layers.
Delamination
Delamination is the separation of layers within the roofing membrane, often caused by improper bonding during installation or environmental factors.
Alligatoring
Alligatoring refers to cracking and patterning of the surface bitumen layer due to aging and loss of flexibility, which leads to potential water penetration.
Surface Erosion
Surface erosion occurs when the top layer of the roofing membrane is worn away by weathering, UV exposure, and other environmental factors, exposing underlying layers to damage. Wind scouring at the corners of the roof is an extremely common problem, resulting in the loss of protective gravel surfacing and the exposure of the bitumen to UV radiation.
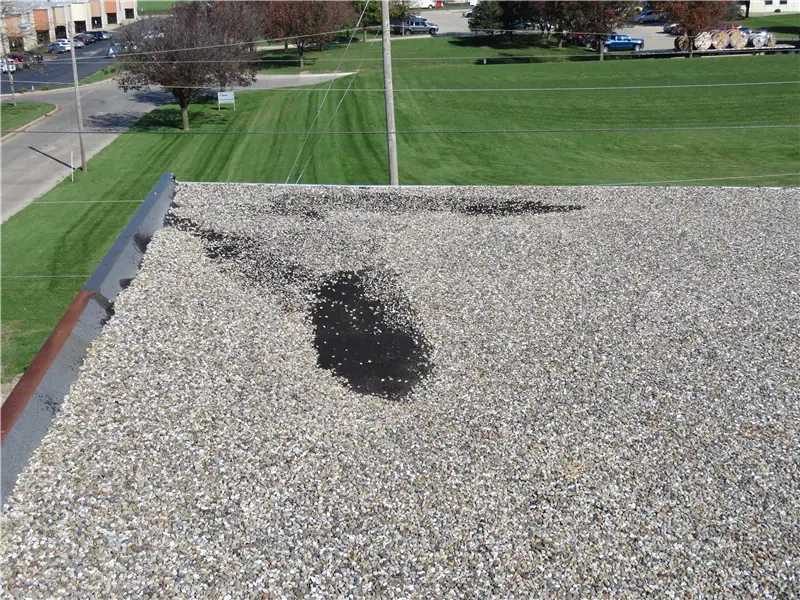
Related Articles
Useful Links for Built-up Roofing Information
1. Recommended for Further Reading: Manual of Low-Slope Roof Systems: Fourth Edition by C.W. Griffin & Richard Fricklas
2. General: For an informative, in-depth general article about various roof systems, see this page at the Whole Building Design Guide site, which is maintained by the National Institute of Building Sciences.
3. Building Codes: “R905.9 Built-Up Roofs” from the 2021 International Residential Code and “1507.10 Built-Up Roofs” from the 2021 International Building Code. Both available on the UpCodes website.
4. Inspection and Maintenance of built-up roof systems: ROOFER: An Engineered Management System (EMS) for Bituminous Built-Up Roofs is an extremely detailed and valuable resource put together by the US Army Corps of Engineers’ Engineer Research and Development Center, and available at the Defense Technical Information Center website.
5. Safety: See this material safety data sheet for health and safety information about the roofing asphalt used in built-up roof systems at the Owens Corning website. This is only an example and other products and brands may be different.
6. Safety: See this material safety data sheet for health and safety information about coal tar pitch at the Durapax website. This is only an example and other products and brands may be different.
7. Safety: See this material safety data sheet for health and safety information about the inter-ply felts used in built-up roof systems at the Johns Manville website. This is only an example and other products and brands may be different.
8. Technical: See this installation guide for insight into how a built-up roof system is put together. Provided by Johns Manville.