Fabric Roofing: Introduction to Tensile Fabric Structures
By Jack Gray, Roof Online Editor • Last updated March 25, 2023
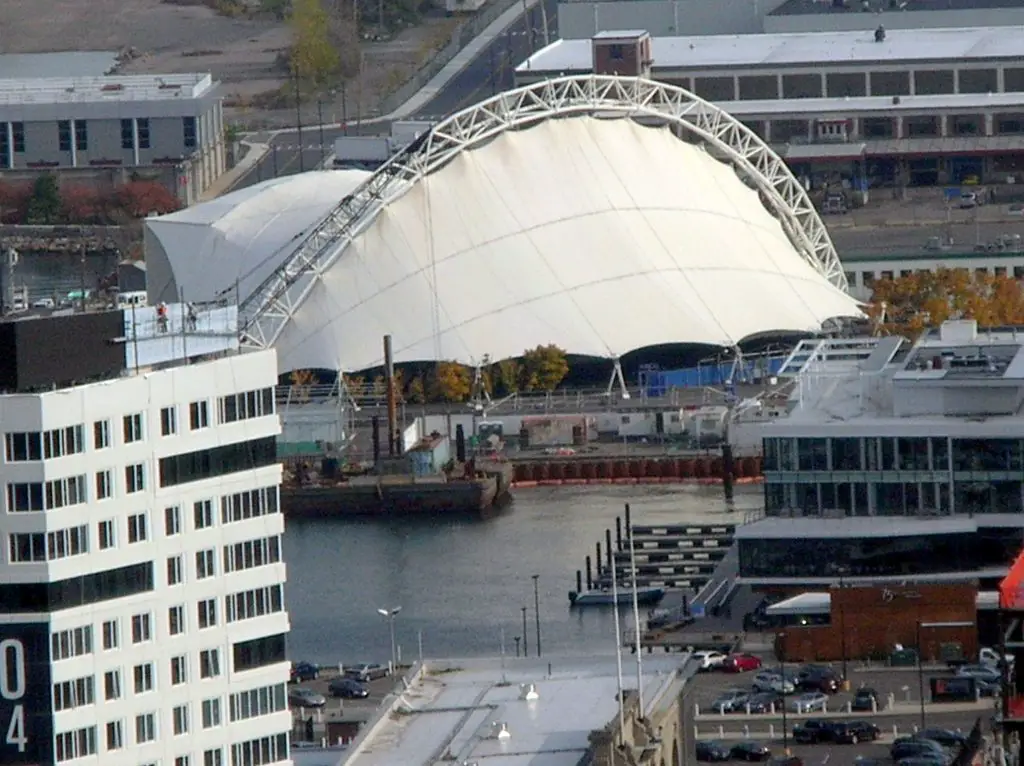
Table of Contents
- Introduction
- Common Applications for Tensile Fabric Roofing
- Fabric Roofing and the Building Code
- History of Tensile Fabric Structures
- Advantages and Disadvantages of Tensile Fabric Roofs
- Design Considerations for Tensile Fabric Roofs
- Materials Used in Tensile Fabric Structures
- Maintenance of Tensile Fabric Roofs
- External Sources & References for Fabric Roofing Information
Introduction
Tensile fabric roofing is a type of roof system that uses tensioned fabric membranes to cover large open spaces without using typical structural support systems (in other words, without having to have a building underneath the roof).
This relatively new type of roofing system has gained popularity in recent years due to its low cost, versatility, and nifty appearance. Fabric roofs can be designed in a variety of shapes and sizes, including domes, cones, and pyramids, and can be endlessly customized to meet the requirements of just about any location.
With their unique combination of functionality, attractiveness, and low cost, and their efficient use of available space, fabric roofs have become the go-to roofing solution for several niche applications.
Common Applications for Tensile Fabric Roofing
Tensile fabric roofing, also known as tensioned membrane roofing, is particularly well-suited for a range of applications where protection from the sun and rain is needed, but money and/or the desirability of substantial construction are primary limiting concerns.
One of the most common uses of tensile fabric structures is in sports facilities, where they provide an open and airy environment for athletes and spectators.
Tensile fabric roofs can also be found in convention centers, shopping malls, parking lots, and airports (and very often at airport parking lots!), where they provide cheap and effective shelter while serving as a visually striking feature that adds to the appeal of the site.
Fabric roofs are not typically designed to serve as a part of a traditional building envelope. They do not significantly restrict the flow of heat and moisture between the interior and the exterior, and they are absolutely inappropriate for most roofing applications.
Fabric Roofing and the Building Code
The International Building Code (IBC) includes several sections that mention tensile fabric structures.
One of the most important sections is Chapter 31, which covers special construction. This chapter includes specific requirements for tensile fabric structures, such as requirements for the materials used in the fabric membrane, the structural design of the support system, and the installation and maintenance of the structure.
Chapter 31 of the IBC is further subdivided into several sections that provide more detailed requirements for specific types of tensile fabric structures.
For example, Section 3102 covers the design and construction of permanent tensioned membrane structures, while Section 3103 covers special event structures, tents, umbrella structures and other membrane structures erected for a period of less than 180 days.
Other sections provide requirements for specific applications of tensile fabric structures, such as sports facilities, exhibition halls, and outdoor events.
In addition to Chapter 31, other sections of the IBC may also apply to tensile fabric structures depending on their specific application and location. For example, Chapter 10 covers means of egress, which includes requirements for exit paths and doors, while Chapter 16 covers structural design and includes requirements for wind loads and seismic design.
History of Tensile Fabric Structures
Strictly speaking, tensile fabric structures have been around for thousands of years. They date back to the nomadic tribes of the Middle East and Asia who used portable tents made from woven fabrics for shelter.
But we’re talking about modern tensile fabric structures here. Modern fabric roofs were developed in the mid-20th century by architects and engineers who were looking for a practical, low-cost way to cover large spans while using a minimal amount of material.
German architect and engineer Frei Otto (1925 – 2015) was a widely-recognized pioneer of tensile membrane structures whose work went a long way toward popularizing their use. He also gets credit for developing many of the design principles and engineering techniques that are still used in tensile fabric structures today.
His work included the construction of numerous large-scale tensile fabric structures, such as the 1972 Munich Olympic Stadium, which featured a roof made of a tensioned membrane supported by a lightweight steel structure.
In the United States, Birdair is a company that has played a major role in the development and popularization of tensile fabric roofing systems. Founded in 1956 in Buffalo, New York, Birdair was one of the earliest companies to specialize in the design, engineering, fabrication, and installation of tensile membrane structures.
Throughout its history, Birdair has been involved in the construction of many high-profile tensile fabric roofing projects, including the 1976 Montreal Olympic Stadium and three out of the four main stadiums at the 2010 World Cup in South Africa.
Birdair has also been instrumental in the development of new materials and manufacturing techniques for tensile fabric structures. The company was one of the first to use Teflon-coated fiberglass as a fabric membrane material, which is now widely used in tensile fabric roofing systems.
Advantages and Disadvantages of Tensile Fabric Roofs
Tensile fabric roofs offer a range of advantages over traditional roofing systems, but they also come with some disadvantages. Here are some key pros and cons of tensile fabric roofs:
Advantages:
- Lightweight: Tensile fabric roofs require less material and structural support than traditional roofing systems, resulting in a lighter and more cost-effective design.
- Customizable: Fabric roofs can be designed in a variety of shapes, sizes, and colors, making them highly customizable and adaptable to a range of applications.
- Aesthetically pleasing: Fabric roofs can provide a uniquely futuristic and visually striking architectural feature.
- Energy-efficient: Fabric roofs allow for natural light and ventilation, reducing energy costs for lighting and cooling.
- Low Cost: Fabric roofs are relatively inexpensive. They require far less material and labor to install than traditional roofs, and they requiring less maintenance and repair over time.
Disadvantages:
- Limited lifespan: While fabric roofs are durable, they have a limited lifespan compared to more traditional roofing systems.
- Maintenance: Fabric roofs do require regular maintenance to ensure that they remain in good condition and continue to provide reliable protection against the elements. Fabric roofs are far more difficult to access than other types of roofing, so roof maintenance and repairs cost far more to perform.
- Design limitations: While fabric roofs offer many design advantages, they are not suitable for many applications or climates.
- Fire risk: Fabric roofs are more susceptible to fire damage than traditional roofing systems, so fire protection measures must be carefully considered and implemented.
Design Considerations for Tensile Fabric Roofs
When designing a tensile fabric roof, several factors must be considered, including the geometry of the structure, the material properties of the membrane, and the loading conditions that the structure will be subjected to. The shape of the structure must be carefully designed to ensure that it can withstand wind, snow, and other environmental loads.
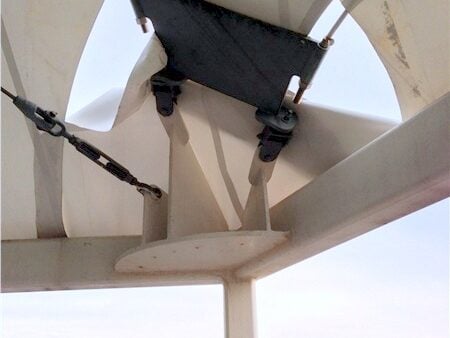
Materials Used in Tensile Fabric Structures
Tensile fabric structures are typically made from high-strength woven fiberglass membranes, to which a protective layer (of various chemistries) is added to resist rain, UV degradation, and other environmental factors. The fabrics are then tensioned over a lightweight support system, which can be made from a variety of materials including steel, aluminum, or wood.
The fabric roofing membranes are usually referred to by the primary chemistry of the weathering layer. These materials include:
- Polyvinyl chloride (PVC) – PVC is a type of thermoplastic polymer that is widely used in tensile fabric membranes due to its high strength, durability, and resistance to weathering and UV degradation.
- Ethylene tetrafluoroethylene (ETFE) – ETFE is a type of fluoropolymer that is lightweight, durable, and highly resistant to weathering and UV degradation. ETFE membranes are often used in applications where high light transmission is desired, such as greenhouses or covered stadiums.
- Polytetrafluoroethylene (PTFE) – Also know commonly as Teflon, PTFE is a type of fluoropolymer that is known for its excellent thermal stability, chemical resistance, and non-stick properties. PTFE membranes are often used in large-scale applications due to their ability to span long distances without the need for support columns or beams.
- Polyethylene (PE) – Polyethylene is a type of thermoplastic polymer that is lightweight, translucent, and highly flexible, although it doesn’t have particularly good UV resistance and degrades in the sun far faster than is acceptable for a roof. PE membranes may be used in temporary structures or as a cheap alternative to other membrane materials.
- Silicone-coated glass fiber – Silicone-coated glass fiber is a type of fabric membrane that is made from woven glass fibers that are coated with silicone to improve the overall strength and durability of the final product. Relative to other types of tensile fabric membranes, these membranes score top marks for tensile strength, fire resistance, and light transmission.
Maintenance of Tensile Fabric Roofs
Tensile fabric roofs require regular maintenance to ensure that they remain in good condition and continue to provide reliable protection against the elements. Here are some key maintenance tasks that should be performed on a regular basis:
- Cleaning – Periodic cleaning of the fabric membrane will likely be necessary to prevent the buildup of dirt, debris, and other contaminants that can affect its performance and appearance, and possibly reduce its lifespan. The cleaning frequency will typically depend on the location of the structure, but a general rule of thumb is to clean the membrane at least once per year. One reason that Teflon (PTFE) is such a popular material for fabric roofs is that very little will stick to it, including dirt.
- Inspection – Regular inspections of the fabric membrane and support structure are important to identify any damage or wear and tear that may need to be repaired. Inspections should be performed at least once per year, but more frequent inspections may be necessary in areas with severe weather conditions. Accessing a fabric membrane roof typically requires special equipment and specifically-trained inspectors. Drones are ideal for inspecting fabric membrane roofs, since no one actually has to get up on the roof, and fabric roof membranes often have few if any components that require anything more than a visual inspection.
- Repairs – Any damage to the fabric membrane or support structure should be repaired promptly to prevent it from worsening and potentially compromising the structure’s integrity. Because the material of a tensile fabric roof is under constant tension, tears, holes, and open seams will get far worse, far faster than other types of roof membrane. Repairs may include patching small tears or replacing damaged components.
- Cleaning and lubrication of tensioning hardware – The tensioning hardware, such as turnbuckles and cables, should be cleaned and lubricated regularly to prevent corrosion and ensure smooth operation.
- Snow removal – In areas with heavy snowfall, it may be necessary to remove snow from the fabric membrane to prevent excessive weight and potential damage to the support structure.
- Retensioning – Over time, the tension on the fabric membrane may loosen, leading to sagging or other issues. It is important to periodically retension the membrane to maintain its performance and prevent damage to the structure.
About the Author
Jack Gray is a principal roof consultant and vice president at the Moriarty Corporation, an award-winning building enclosure consultant firm founded in 1967. He is also the editor of the Roof Online website.
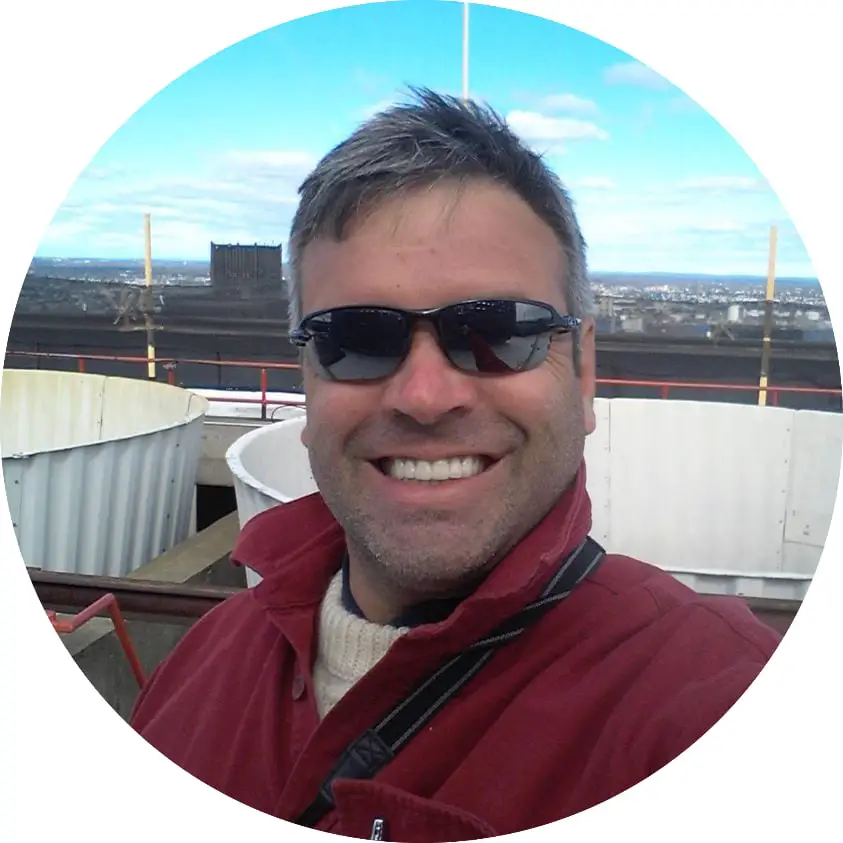
Mr. Gray has worked in the roofing industry for over 25 years, with training and practical experience in roof installation, roof inspection, roof safety, roof condition assessment, construction estimating, roof design & specification, quality assurance, roof maintenance & repair, and roof asset management.
He was awarded the Registered Roof Observer (RRO) professional credential in 2009.
He also served as an infantry paratrooper in the 82nd Airborne Division and has a B.A. from Cornell University. Read full bio.
External Sources & References for Fabric Roofing Information
1. General: A short history of the use of Teflon fabric in the construction industry is available on NASA’s Technology Transfer Program’s website. The article focuses mainly on Birdair’s contributions to the development of the technology.
2. General: “Fabric Architecture Magazine” is produced by the Advanced Textiles Association. The site is searchable, and there is a great deal of information available.
3. General: A generally informative article on Teflon is available on this Wikipedia page.
4. Chemical Compatibility of PTFE: “PTFE and Teflon Chemical Compatibility Chart“. Available on the website of CP Lab Safety.
5. Technical: See this product data page for the technical characteristics of PTFE at the Boedeker Plastics website. This is only an example and other products and brands may be different.