Rules of Good Roof Design
By Jack Gray, Roof Online Editor • Published November 8, 2023
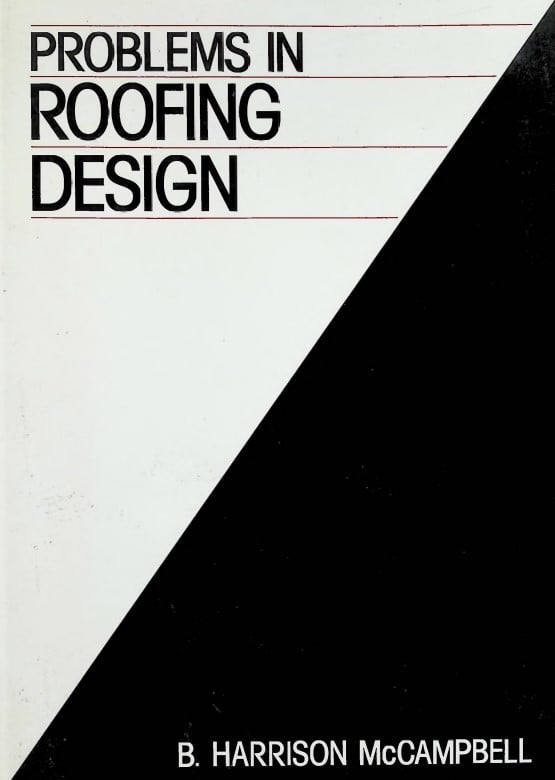
Introduction
The following guidelines were taken from the book Problems in Roofing Design by B. Harrison McCampbell.
This book examines 101 of the most common roof design issues. Each problem is examined in a separate section. These sections describe the consequences of a particular example of poor roof design and explains how to resolve it, with photographs and drawings that illustrate the problem and its solution.
Although this book was published in 1992 and many roofing materials and installation techniques have changed since then, the principles of roofing that it presents are still valid today (and may possibly be eternal).
Studying this book is an excellent way for roofing novices (or even experienced roofers and specifiers who have developed bad habits) to gain a proper fundamental understanding of roofing that can be applied when designing, installing, or inspecting roofs.
We keep this book in our own roofing reference library and we strongly recommend it to anyone who installs, inspects, repairs, or maintains roofs.
If there are any copies available, you may be able to find it on Amazon.
The rules presented below apply chiefly to low-slope roofs, but the book itself does examine some problems with pitched roofing materials such as asphalt shingles or tile roofing.
General Rules of Good Roofing Practice
“There are a few general rules of good roofing practice that should be adhered to during the design phase:
1. The first step toward having a successful roof is to have good positive drainage. Build the slope into the roof through the incline of the substrate at a rate of at least 1/4″ per foot. One-half inch should be enough on the high side for most low-sloped roofs. Anything steeper than that will take extra care in the selection of materials and methods of installation, so beware.
2. Keep roof drains away from column lines. It is always convenient to hide downspout piping within the web of a steel column, but, unfortunately, the top of the column is at the high point of the roof. The best location for the roof drain is at mid-span of the structural member where the low point is, or along an exterior wall with the structure sloping down toward the wall. Then you could use “crickets” or “saddles” to divert the water in a positive fashion along the walls to each roof drain.
3. Try to avoid using gravel on your roofs. Gravel, if not already, is soon to be a limited-quantity item. There is only so much. Not unlike water, it has always been around. But everything has a limit. Smooth-surface roofs are lighter in weight and easier to maintain. If you use a coating on the roof, that also serves two purposes—it eases the thermal load on the immediate roof surface and it allows the maintenance to be generally limited to the coating and not the roofing material below.
4. Use a flexible flashing material. That is where movement occurs. Almost every manufacturer now offers some type of material that allows for more movement than the field material. Utilize it. And when specifying the wall flashing for built-up roofs, make sure to call for the sheet flashing material used on a wall 24″ or higher to be “strapped.” This means that the flashing is to be installed in a vertical fashion, no more than 36″ wide. This keeps the roofer from using long horizontal applications the usually sag due to the inability of the material to support itself. It is also due to the fact that too large a piece of flashing allows the asphalt to cool prior to installation, resulting in a condition where the flashing is not fully adhered to the wall, causing blistering. The material can be installed in a horizontal fashion on walls under 24″ in height, but make sure to specify a maximum flashing length of 10′-0″ to keep the asphalt hot for proper adhesion.
5. Use lead boots and caps on vent pipes. Keep roof maintenance down.
6. Specify cast iron assemblies on roof drains. PVC will not last as long. The amount of money spent over the life of a roof drain for cast iron is limited, whereas the amount spent in constantly replacing anything else is not.
7. Provide at least a 4″ flange on gravel stop and pitch pocket sheet metal (minimum 24 gauge). This allows ample space to cover the fasteners properly.
8. Don’t hesitate to use gutters. Control water when possible.
9. Keep curb and counterflashing heights at an 8″ minimum.
10. Keep a minimum of 18″ between curbs, pipes, and edges of the roof.
11. Roofing should be watertight without counterflashing. Seal the top edge of flashing material, especially if the metal counter-flashing above is surface mounted.
12. Whenever possible, specify that the roofing material is installed prior to the installation of the curbs, whether factory-installed or field-fabricated. This way the curb is “sandwiched” in roofing material. Nonetheless, consult manufacturer’s recommendations.
13. Try to change the shape of a roof penetration to avoid the use of a pitch pocket. But if you must use a pitch pocket, keep the size down to where the outer edge of the pitch pocket is 2″ from the outer edges of the roof penetration. Too much mastic will only become a maintenance headache.
14. Don’t rely on manufacturer’s recommendations from one printed sheet to supply your job with all necessary information pertaining to your particular design. The architect may believe that the manufacturer shows and controls all details to protect itself. That is why you have to take control yourself and ask questions of your selected manufacturer or an independent roofing consultant as you design. It will involve them early on and could possibly save money in the long run.
15. As you are designing the roof on your next new building, keep in mind that the roofing system will need maintenance, repair, and eventually, replacement. Don’t design-in problems that can save you money now but cost you money down the road, as in low curb and counterflashing heights, thin one-piece counterflashing that is worthless once it is turned up, and so on.
16. Finally, pay attention to the sheet metal details. Most of the time, the sheet metal gets neglected, yet it carries a great amount of responsibility. Almost always, sheet metal is called out to terminate and/or counter-flash a roofing material. So don’t try to save money on such a critical area, and don’t be afraid to call for a thicker minimum than that required by code. Remember, the code is simply saying that, for example, 26 gauge is the least amount of thickness needed for the job. In some situations, that may not be enough.”