Roofing Adhesives • Important Facts and Guidelines
By Jack Gray, Roof Online Editor • Updated March 18, 2024
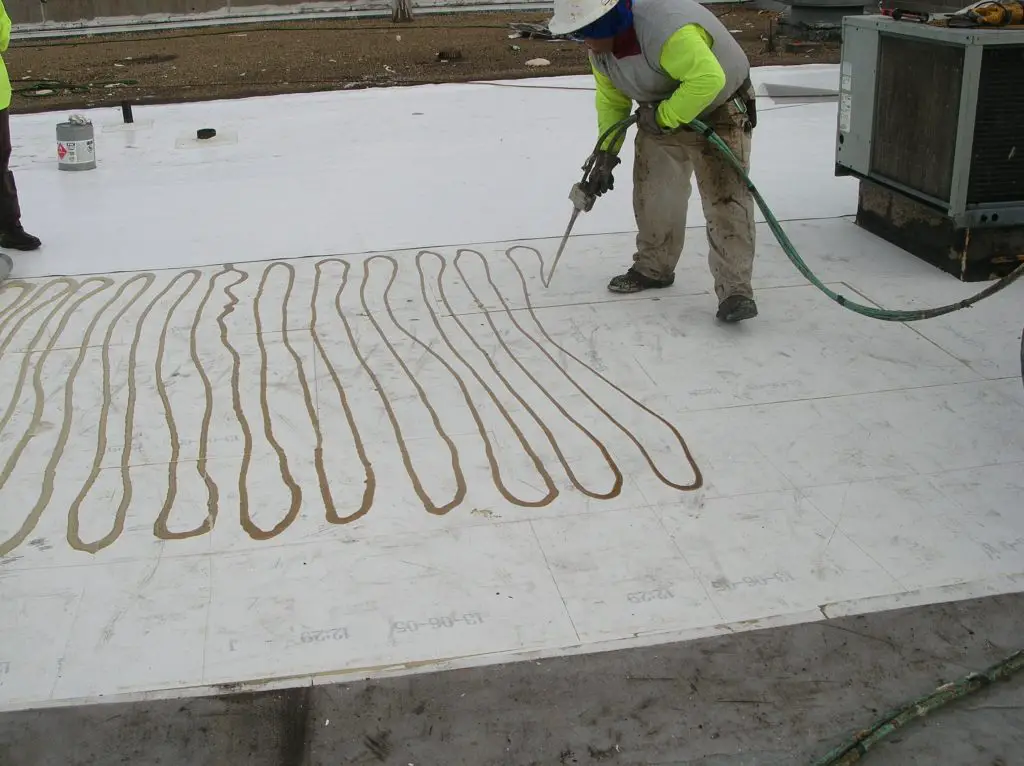
Table of Contents
- Construction Definition – Adhesive
- How Adhesives Are Used in Roofing
- Roofing Adhesive Formulations Change Often
- Roofing Adhesive Application Temperatures
- Related Articles
- External Sources & References for Roofing Adhesive Information
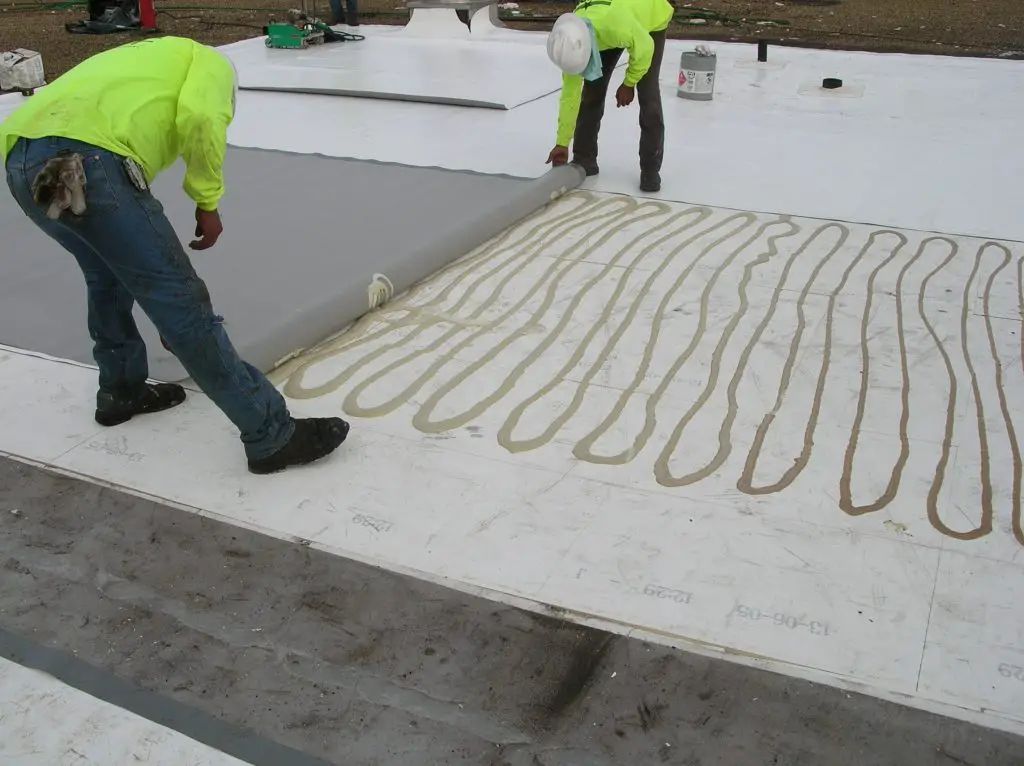
Construction Definition – Adhesive
A substance used to chemically bond two surfaces together. Contrast with fasteners, which attach building components mechanically.
How Adhesives Are Used in Roofing
Adhesives play several critical roles in roofing. In particular, adhesives are vital in single-ply low-slope (“flat”) roof systems which use EPDM, PVC, or TPO membranes, and often hold the entire system together.
Adhesives Instead of Roofing Fasteners
In flat roof systems where structural concrete decks make using mechanical fasteners (specialized roofing screws) impossible or impractical, adhesives are used to attach the bottom layer of insulation (and thus the entire system) to the roof deck.
Even with other deck types such as ribbed steel, where fasteners can be used, it’s fairly common for the base layer of insulation to be mechanically fastened to the deck while adhesives are used to attach all of the other layers of the roof system.
Adhesives can be used to bond multiple layers of insulation board to each other, adhesives can be used to bond a cover board layer to the insulation, and adhesives can be used to attach the waterproof roof membrane to the cover board.
Adhesives in Single-Ply Roof Membrane Systems
Roofing adhesives are used extensively in single-ply membrane roofs. They are used to secure the insulation, the cover board, the field membrane, the flashings, and the entire roof system itself to the roof deck.
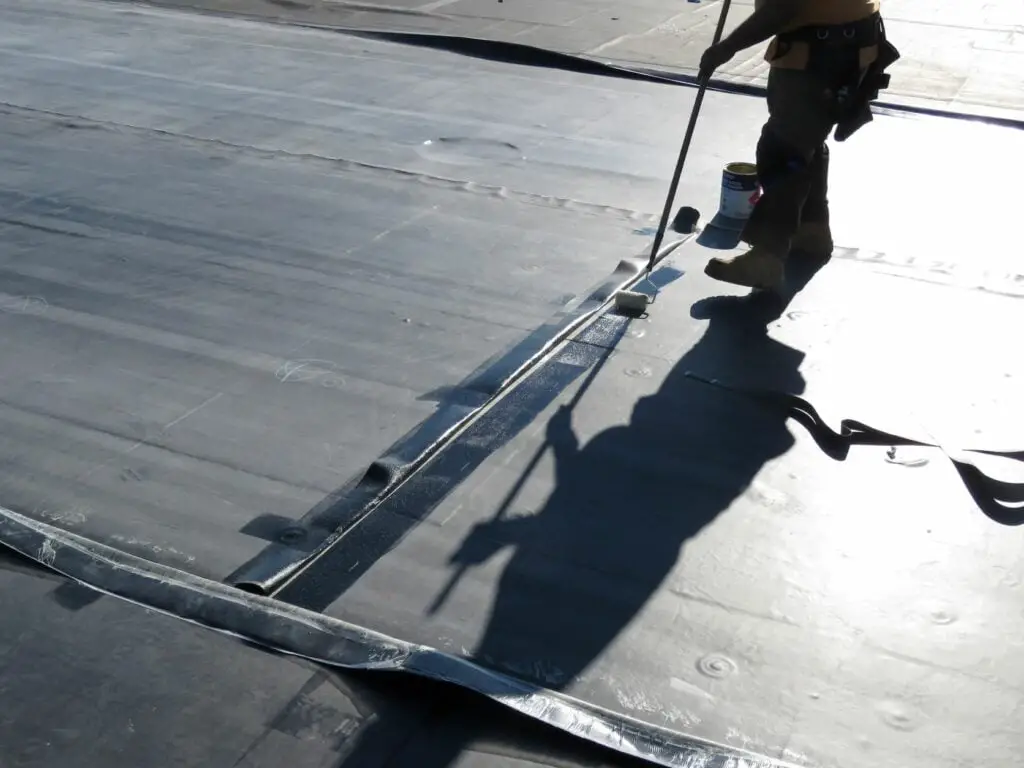
When adhesives are used to attach an entire single-ply roof membrane to the underlying insulation or insulation cover board, the roof system is known as a “fully-adhered membrane system”.
“Fully-adhered” only refers to the attachment of the membrane itself, and the phrase is used to distinguish this attachment technique from mechanically-attached membrane systems (which use batten strips and screws) and ballasted membrane systems (which are weighted down with stones or pavers).
A fully-adhered system may still use fasteners instead of adhesives to hold the cover board and insulation layers together, as well as to secure the entire roof system to the roof deck.
The most common roof insulation adhesive is two-part polyurethane foam, applied using special pressurized applicator systems.
Although fleece-back roof membranes are often installed in polyurethane foam, most single-ply membranes are glued down with one-part membrane adhesives; these are non-foaming products which are usually applied with rollers.
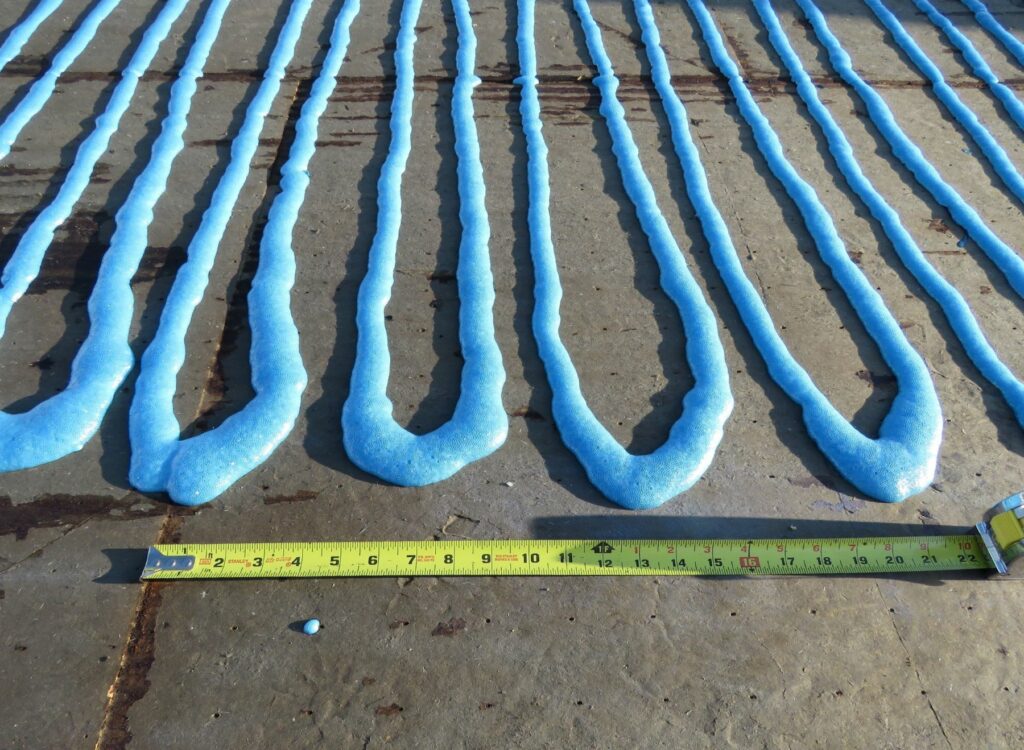
Adhesives in Built-Up Roofing
Specially-formulated roofing adhesives are almost never used in built-up roofing, unless the built-up roof membrane is actually constructed using cold process adhesives (see the Modified Bitumen section below).
The hot asphalt or coal tar pitch that makes up the roofing membrane also functions as an adhesive, bonding the membrane to the cover board during installation. Although fasteners are used now, for many years it was even common to use strips of asphalt hot-mopped onto the roof deck to attach the base layer of the insulation (typically perlite fiberboard) and thus the entire roof system.
When repairing old asphalt built-up roofs, asphalt-based cold-applied adhesives, which come in buckets, may be used, although for large repairs it’s better to get a kettle out to the site and make the repairs with hot asphalt.
Because it’s becoming harder and harder to find a roofer who still has a kettle and works with hot asphalt, cold-applied adhesives may be your only option in some areas.
When repairing an asphalt built-up roof using cold-applied adhesive, the repair area should be thoroughly cleaned with any gravel surfacing scraped off. The adhesive should then be applied per the manufacturer’s instructions (typically poured on and then squeegeed for a proper coverage rate). Although the gravel can then be re-applied to the coated area, it’s a better practice to set a patch made out of modified bitumen or even regular roll roofing into the adhesive as a cap sheet.
Adhesives in Modified Bitumen Roof Systems
Modified bitumen systems, which are often installed using hot asphalt to bind the layers together, may instead use cold-applied adhesives. Cold-applied adhesives are preferable to hot asphalt because you don’t have to worry about the hot asphalt application temperature being too cool to properly bond with the modified asphalt. This is a very common issue and a big cause of blisters in modified bitumen roofs.
Cold-process adhesive products are typically asphalt-based, and can be delivered to the roof from the factory in buckets and applied at the ambient temperature, so there’s no need to melt asphalt in a kettle and then pipe it to the roof.
They are poured out and spread with squeegees, and the roof components are set into them like they would be with hot asphalt.
Normal cold-applied adhesive formulations are known for having a very strong odor, which continues for days after the application while the adhesive cures. Great care needs to be taken to seal penetrations through the roof deck to prevent the odor from getting into the building.
Some newer formulations are designed to be “low-odor” and don’t release the volatiles that cause these odors.
Adhesives in Steep-Sloped Roofing
Steep-slope roofing (shingle, tile, slate, and some metal panel roofing) will almost never use adhesives as the primary attachment method for the roof covering, with the exception of the relatively new use of polyurethane foam adhesive to replace mortar as a method of attachment for clay and concrete tile roofs.
This is not to say that adhesives play no role in steep-slope roofing. Roofing adhesive, applied with a caulk gun or trowel, is an important component of asphalt shingle roofs.
Virtually all asphalt shingles manufactured today come with a self-sealing strip of adhesive that is intended to bond the shingle tabs to the shingles below them.
This greatly reduces the effects of wind-uplift and the damage to the shingles it causes, which has always been an issue with asphalt shingles when compared to more rigid materials like wood or tile.
The failure of this self-sealing strip to properly self-seal is one of the most common complaints you will hear when you hear people complaining about shingle performance. This failure happens most often when shingles are installed in cold weather, but can be due to manufacturing defects.
On-site application of roofing adhesive can fix this problem.
Supplementary applications of roofing adhesive, in the form of asphaltic roof cement, is very often used to prevent wind-uplift of the shingles. This is done by carefully applying dabs of the adhesive (roof cement) under the ends of the shingle tabs of every shingle on the roof.
A quarter-sized spot roof cement is typically applied every couple of inches across the shingles, about an inch higher than the bottom end of the overlapping shingle tabs.
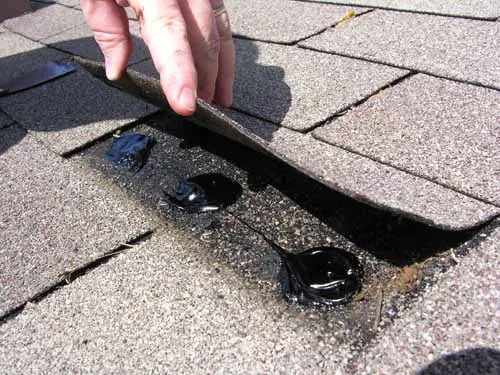
Many roofing contractors will not do this, as it’s extremely time-consuming (and therefore expensive) and many homeowners do not think to ask them to do it (or want to pay for it). But by preventing wind damage, this technique can greatly increase the life expectancy of the roof.
Some professional roof consultants will even specify two spots of roof cement under every single shingle tab on the roof, because it is so effective at preventing long-term damage.
The tabs of the rake edge shingles (the shingles along the sloped edges at the ends of the roof) should get an extra application of roof cement, because, out of the entire roof area, these locations are almost always subjected to the strongest wind-uplift forces.
In addition to addressing wind uplift issues, roof adhesives are used to make minor roof repairs or emergency repairs on all types of shingle roofs, when proper repairs are considered too expensive or can’t be done immediately.
Roofing Adhesive Formulations Change Often
Roofing adhesive products, as with roof coatings and sealants, are subject to fairly frequent reformulations and chemical industry advances. It’s important to realize that this can affect what weather conditions, especially temperature, that the adhesives can be successfully used in.
It’s pretty common to find that the newest version of a roofing adhesive brand or product has specifications that are slightly different from a previous version that you might be familiar with. There may be different substrate compatibility guidelines, a different recommended application rate, or a different recommended application temperature range.
Always read the product data sheet before using a roof adhesive, even if you’re familiar with the brand.
Roofing Adhesive Application Temperatures
Reading product literature and strictly following manufacturer recommended guidelines is critical when using roofing adhesives. Many other roofing products give you a lot of leeway during installation, but adhesives don’t.
If you do not apply roofing adhesive within the recommended temperature range, you run the risk that the adhesive will not be able to bond properly with the substrate before it sets and becomes inert (usually within minutes).
Adhesive application temperature ranges are typically between 35 and 95 degrees Fahrenheit.
Roofing adhesive manufacturers have recently started making more cold-tolerant products which can be applied in temperatures as low as 30 degrees.
A long-time rule of thumb in the industry, however, is that you should never apply roofing adhesives when the temperature is below 40 degrees. If you can stick to that (stick to that!) policy, you should.
Related Articles
- Asphalt Shingles: Useful Information Guide
- Best Roof Shingles Guide • Top 7 Shingle Brands
- Roof Decking
External Sources & References for Roofing Adhesive Information
1. General: Adhesive industry news and press releases can be found on the Adhesive and Sealant Council website.
2. Insulation Adhesive: “JM Two-Part Urethane Insulation Adhesive“. See this product data sheet at the Johns Manville website for information about a typical insulation adhesive used on low-slope roofs. This is only an example and other products and brands may be different.
3. Modified Bitumen: “Cold Adhesive SBS-Modified Bitumen Roofing Applications” is a basic overview put together by the Asphalt Roofing Manufacturers Association.
4. Tile Roofs: See Dupont’s TILE BOND™ Roof Adhesive YouTube video to get an idea of how polyurethane foam adhesive is used in the securement of tile roofs.